Digitalizacja jest kluczem do wykonywania bardzo szybkich i precyzyjnych napraw. Jest to szczególnie ważne, jeśli oryginalne części są trudne do pozyskania. Z tego powodu niektóre firmy zaczęły same wytwarzać nowe części do szerokiego zakresu maszyn wirujących jako odlewy, wykorzystując technologie produkcji addytywnej, przyrostowej, czyli druku 3D.
Producenci urządzeń w modelu OEM robią wszystko, co w ich mocy, aby dostarczyć klientom kompleksowy zestaw części zamiennych do swoich wyrobów. Jednak gdy dany sprzęt jest już eksploatowany od kilku dekad, jego producent OEM może nie być już w stanie dostarczyć klientowi odpowiedniego wsparcia. Być może firma ta została już wykupiona przez inną lub zaprzestała produkcji części zamiennych do danej maszyny i nie posiada już żadnych części w magazynie. Wymiana i naprawa podzespołów sprzętu jest ważna dla utrzymania go w dobrym stanie technicznym oraz dla zachowania przy jego pomocy wydajności produkcji na wymaganym poziomie. Gdy chodzi o większe podzespoły maszyn i urządzeń, to ich rola jest często bardziej kluczowa. Dokonywanie napraw w wymaganym czasie jest bardzo ważne ze względu na negatywne skutki przestojów.
Skanowanie laserowe w produkcji precyzyjnej
Wykonanie zestawu rysunków technicznych 3D jest obecnie mniej czasochłonne dzięki wykorzystaniu przenośnych skanerów laserowych, które potrafią dokonywać szybkich i bardzo dokładnych pomiarów części rzeczywistych. Przy wytwarzaniu części zamiennych do kluczowych maszyn i urządzeń w zakładzie szybkość odgrywa główną rolę. Wykorzystując skanery laserowe najnowszej generacji, inżynierowie mogą zebrać 480 000 punktów danych na sekundę. Siedem przecinających się linii światła laserów zapewnia dokładny przechwyt wymiarów obiektów o nawet najbardziej złożonej geometrii.
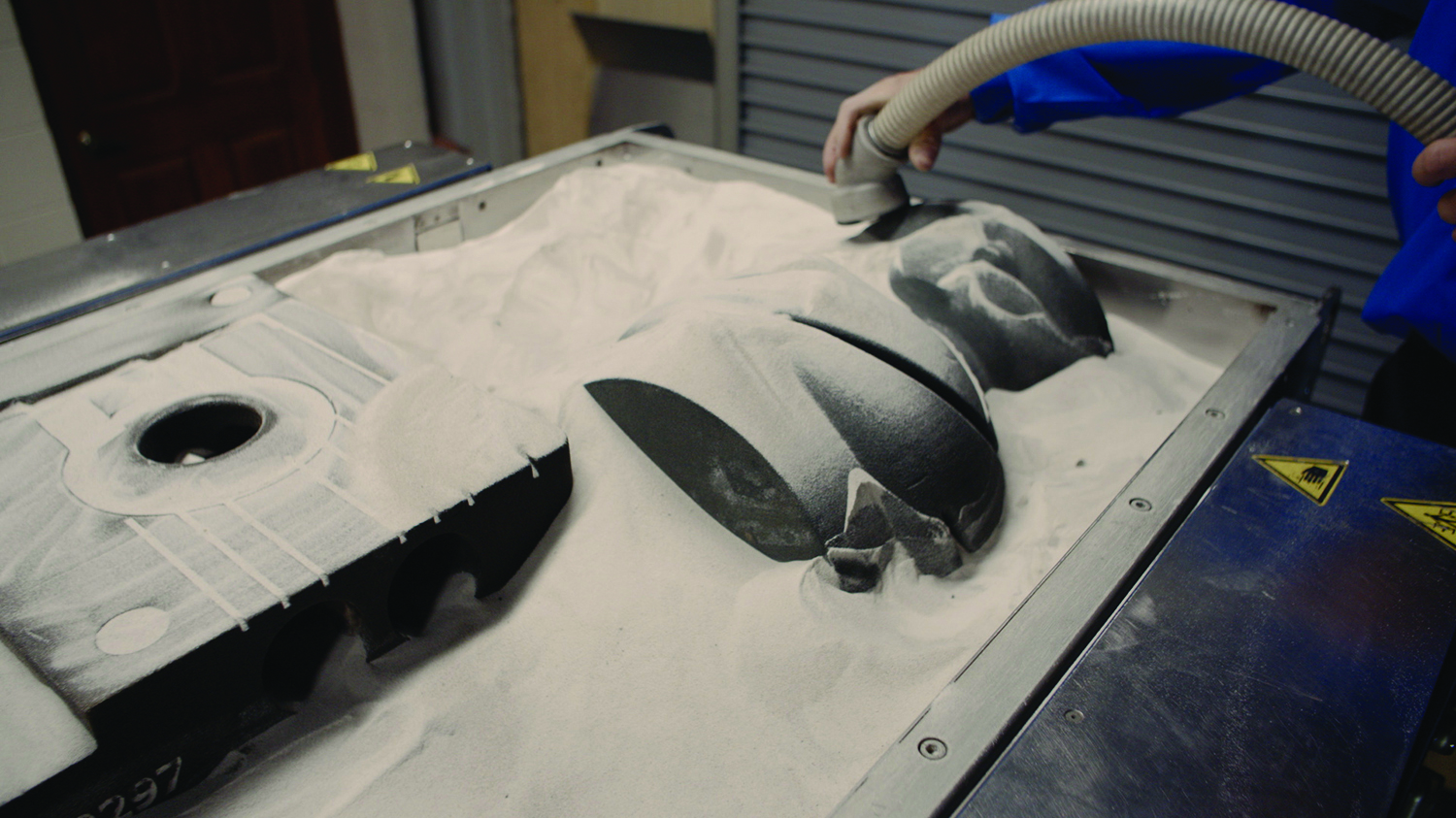
Prace inżynierów w miejscu zainstalowania sprzętu
W przypadku sprzętu, którego nie można łatwo przenieść, inżynierowie firmy OEM mogą odwiedzić zakład klienta, aby udzielić mu specjalistycznych porad i wykonać pomiary niezbędne do stworzenia nowych rysunków technicznych. Wykorzystują oni współrzędnościowe maszyny pomiarowe (WMP, ang. coordinate measuring machine ? CMM) i skanery laserowe do zebrania niezbędnych danych na miejscu. Sprzęt ten umożliwia uzyskanie powtarzalności wymiarów z dokładnością 0,025 mm.
Po zebraniu podstawowych danych dotyczących wymiarów inżynierowie projektanci mogą dokładnie dopracować projekt nowego podzespołu. Na przykład mogą dopracować geometrię wirnika turbiny, aby mieć pewność, że tolerancje wymiarów zostały zoptymalizowane.
Projektanci mogą także dokonać zmian w oryginalnym projekcie, aby umożliwić zmiany jego zastosowania lub wymaganych parametrów technicznych.
Produkcja addytywna form odlewniczych
Tradycyjnie odlewanie nowego podzespołu obejmowało wykonanie drewnianego wzorca oryginału i umieszczenie go w skrzynce formierskiej z piaskiem. Proces ten jest bardzo czasochłonny i może trwać nawet kilka tygodni. Ponadto mogą tu wystąpić znaczne niedokładności wykonania odlewu, szczególnie gdy wzorce drewniane był przechowywane dłuższy czas i uległy zniekształceniu.
Obecnie projektanci mogą eksportować rysunki techniczne w postaci pewnej liczby plików cyfrowych, które mogą następnie zostać wykorzystane przez wiele obrabiarek i robotów. Jedną z metod jest zastosowanie drukarki piaskowej 3D, która wykorzystuje te dane do bardzo szybkiego wykonania formy odlewniczej nowego podzespołu. Wykorzystując warstwy piasku i kleju, drukarka 3D może wykonać formę odlewniczą wytrzymałą na wysokie temperatury stopionego metalu, który uformuje nowy podzespół.
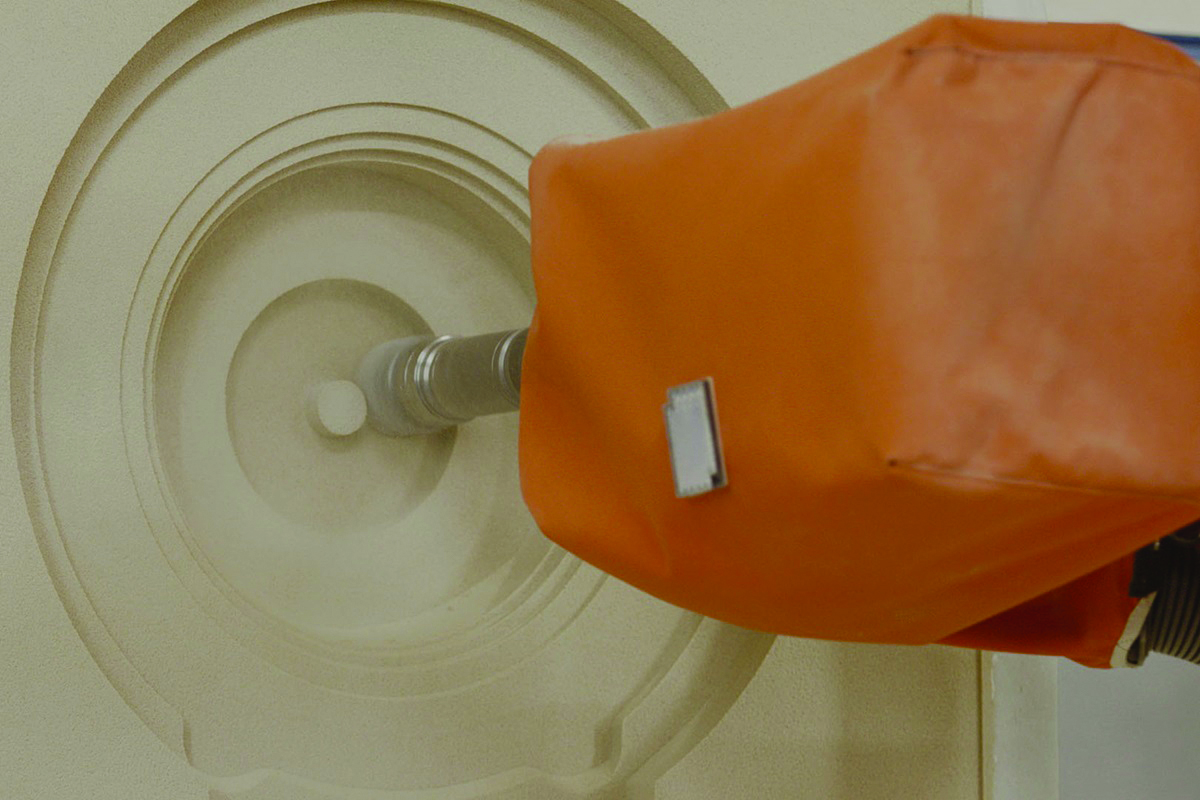
Oszczędność czasu dzięki technologii odlewania bezwzorcowego
W procesie tworzenia formy inżynierowie projektanci wykorzystują obliczeniową dynamikę płynów do przewidywania przepływu gazów w formie podczas wlewania do niej płynnego metalu. Konieczne jest, aby gazy te miały skuteczne drogi ujścia, ponieważ pęcherze gazu uwięzione w odlewie mogą spowodować osłabienie nowego podzespołu. Odpowietrzenia odlewów mogą być zawarte w rysunkach 3D wykonanych w programach CAD i łatwo włączone do procesu drukowania w formie piaskowej.
Proces ten wymaga ok. 48 godzin do zakończenia, jednak w zależności od wymiarów odlewanych podzespołów można drukować jednocześnie wiele odlewów, co sprawia, że proces ten jest bardziej wydajny. Inną metodą tworzenia form odlewniczych, często stosowaną do wytwarzania obudów, jest wykorzystanie dwóch połówek formy, zwanych górną i dolną (the cope and the drag). Połówki te są składane razem, aby utworzyć gotowy kształt odlewu. Dziś proces ten rozpoczyna się od wykonania trwałego bloku z piasku, który jest obrabiany maszynowo przy wykorzystaniu robota frezującego CNC, w celu stworzenia precyzyjnej formy odlewniczej, według rysunków 3D wykonanych w programie typu CAD.
Aby wyprodukować drewniany wzorzec dla piaskowej skrzyni odlewniczej metodą tradycyjną, potrzeba od 2 do 6 tygodni, w zależności od złożoności formy wzorca. Wykorzystując drukarkę piaskową 3D, eliminuje się konieczność wyprodukowania wzorca, zaś forma odlewnicza jest drukowana bezpośrednio i gotowa w czasie od 48 do 60 godzin. Obróbka maszynowa precyzyjnej formy z bloku piasku wymaga od 2 do 4 godzin.
Posiadanie własnej odlewni w zakładzie ma kluczowe znaczenie dla wytwarzania nowych części zamiennych. Odlewnia taka może wykorzystywać 100 różnych stopów do wykonywania odlewów o masie do 450 kg. Projektanci określają dokładny skład stopu metali na podstawie danego podzespołu i jego zastosowania. Posiadając doświadczonych specjalistów od metalurgii, firma może oferować nowe podzespoły i części zamienne, które są trwalsze od oryginałów.
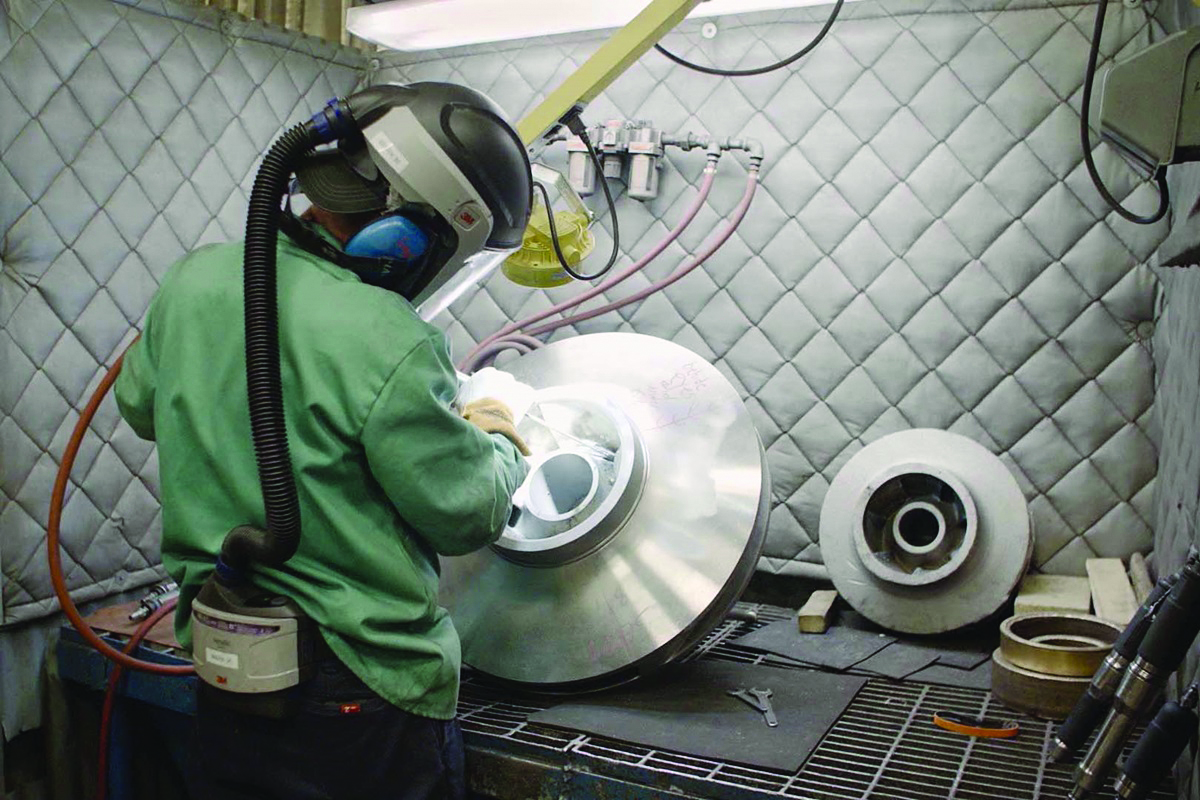
Większa precyzja dzięki obróbce maszynowej CNC
Po utworzeniu podstawowych bloków konstrukcyjnych nowego podzespołu pracę przejmuje warsztat, który określa ostateczne wymiary. Warsztat ten jest wyposażony w pionowe tokarki CNC do produkcji wirników turbin, mis i czasz oraz tokarki poziome, frezarki i szlifierki, co pozwala na produkowanie złożonych podzespołów dla klientów. Ponadto warsztat realizuje obszerne procedury kontroli jakości i posiada odpowiedni do tego sprzęt, dzięki czemu każda część zamienna jest wytwarzana zgodnie z najwyższymi standardami.
Kontrola jakości zwiększa niezawodność
Centrum serwisowe może ponadto wykonywać obróbkę cieplną, sporządzać certyfikowane atesty składu chemicznego i właściwości mechanicznych (certified material test report ? CMTR), wykonywać analizy chemiczne, testy mechaniczne w pewnym zakresie oraz badania nieniszczące (non-destructive testing ? NDT). Zapewnia to niezawodność wytwarzanych części zamiennych oraz ich zgodność ze specyfikacjami klientów.
Jennifer Cardillo jest dyrektorem ds. marketingu i komunikacji na obszar Ameryki
Pn. i Pd. w firmie Sulzer. Specjalizuje się w usługach związanych z maszynami wirującymi.