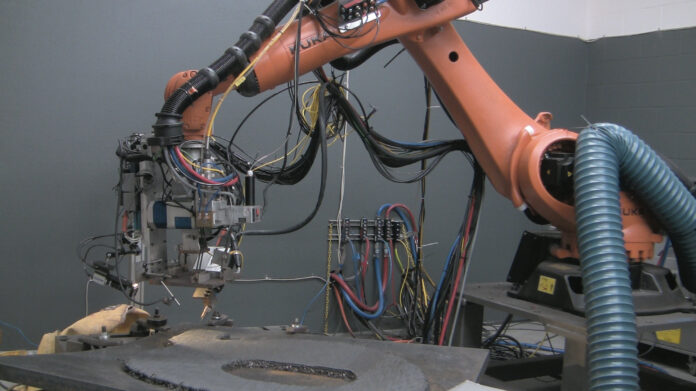
Wytwarzanie przyrostowe wpływa na zmianę myślenia inżynierów i projektantów części. W tym obszarze z powodzeniem wykorzystywane są roboty, które sprawiają, że produkcja addytywna staje się dokładniejsza, szybsza i efektywniejsza.
Produkcja addytywna zmienia nie tylko sposób, w jaki tworzymy obiekty. Zmienia również sposób, w jaki myślą inżynierowie i konstruktorzy, ponieważ mogą oni wówczas zapomnieć o ograniczeniach wynikających ze stosowania konwencjonalnych metod wytwarzania i otworzyć się na nowe możliwości konstrukcyjne. Możliwości te przyczynią się do wzrostu wartości rynku obróbki addytywnej do 17 miliardów dolarów do 2020 roku. Istnieje wiele procesów obróbki addytywnej, takich jak stereolitografia (Stereolithography Apparatus ? iSLA), selektywne spiekanie laserowe (Selective Laser Sintering ? SLS) oraz osadzanie topionego materiału (Fused Deposition Modeling ? FDM).
Wszystkie te metody są wspomagane przez systemy CAD (Computer Aided Design). Dane używane są do tworzenia obiektów 3D, które powstają metodą warstwa po warstwie z materiałów ciekłych, proszków, arkuszy lub innego typu materiałów.
Wykorzystując technologię wytwarzania addytywnego, możliwe jest nawet odtworzenie ludzkiej tkanki. Możemy budować różne struktury, począwszy od zastosowań dentystycznych do zaawansowanych podzespołów stosowanych w lotnictwie, budowy mostów, a nawet dzieł sztuki.
Roboty i manipulatory sprawiają, że jest to możliwe. Roboty nie tylko pozwalają na stosowanie obróbki addytywnej, ale także są używane w drukarkach 3D (również zrobotyzowanych), w zautomatyzowanych procesach obróbki poprocesowej, a nawet pozwalają architektom na nowe sposoby wizualizacji obiektów, które budują.
Warstwa po warstwie
W siedzibie firmy Midwest Engineered Systems Inc. (MWES), w mieście Waukesha, w stanie Wisconsin, do tworzenia skomplikowanych części metalowych stosuje się aktywną obróbkę laserem. Stworzenie takich części inną metodą byłoby niezwykle trudne, jeśli nie niemożliwe. W procesie wykorzystywany jest sześcioosiowy manipulator, a sam proces wykorzystuje metodę osadzania topionego materiału oraz obróbkę laserową do tworzenia części metodą warstwa po warstwie. Z egzotycznych materiałów w sposób szybki i precyzyjny tworzone są części prototypowe oraz niewielkie serie kosztownych i skomplikowanych części.
MWES ma ponad 25-letnie doświadczenie w integracji złożonych systemów. Dzięki temu udało się rozwinąć proces zaprezentowany na międzynarodowych targach technologii wytwarzania w roku 2016. Podczas targów zaprezentowano proces produkcji śruby napędowej.
MWES nazwało swój system ADDere. Słowo to pochodzi z łaciny i oznacza dodawanie. Proces ten podobny jest do procesu zwanego WLAM (wire and laser additive manufacturing), w którym metalowy drut jest podawany w obszar, gdzie zostaje stopiony przez laser i spojony z podłożem. Materiałem dodawany i podłoże stają się jedną częścią. Różnica między tymi dwoma procesami polega na tym, że proces MWES wykorzystuje podgrzany drut.
? ?Podgrzewamy drut do momentu, w którym jego czoło zaczyna się topić? ? twierdzi Scott Woida, prezes i założyciel firmy MWES. ? ?Jako że materiał drutu jest już stopiony, używamy lasera do stopienia podłoża w celu stworzenia silnego połączenia między tymi dwoma materiałami. Jeżeli laser rozgrzewa jedynie podłoże, zużywamy mniej energii. Stosowanie gorącego drutu pozwala na dodanie większej ilości materiału przy jednoczesnym zmniejszeniu ilości dostarczanego ciepła?.
Proces powstawania części zawsze zaczyna się od stworzenia podstawy. W części prezentowanej na targach ? śrubie napędowej ? podstawę stanowił cylinder.
? ?Za podstawę może posłużyć również część samego obiektu. Możemy również odciąć podłoże na końcu procesu i uzyskać część w całości stworzoną metodą addytywną? ? twierdzi Woida. ? ?Musimy jednak od czegoś zacząć. Może to być nawet coś tak prostego jak niewielki kawałek stali?.
Drut, laser i robot
Podstawowe części systemu to bardzo precyzyjny manipulator przemysłowy, laser, zintegrowany podajnik drutu MIG, głowica laserowa, jak również system sterowania MWES. Proces składa się z aktywnego sterowania głowicą oraz dynamicznego pomiaru osadzanego materiału w celu dokładnego monitorowania procesów przed, w trakcie obróbki oraz po obróbce.
Dane CAD są importowane do oprogramowania CAD/CAM, gdzie są przygotowywane do procesu addytywnej obróbki. Część jest następnie dzielona na warstwy i generowane są ścieżki ruchu robota. Informacje mogą być dodawane do procesu w sposób automatyczny lub manualny. Generowana ścieżka i informacje na temat procesu są przetwarzane w części zwanej postprocesorem i automatycznie przekazywane do sterownika robota. Następnie robot, wykorzystując program, buduje część warstwa po warstwie. Zastosowania takiej metody obróbki to:
- tworzenie części prototypowych
- budowa niewielkich serii produkcyjnych
- tworzenie części zamiennych
- tworzenie części przeznaczonych do renowacji
- pokrywanie powierzchni.
System ADDere wykorzystuję 6-osiowego robota o dużym zasięgu, który zapewnia elastyczność i duże pole robocze. Manipulator współpracuje z wieloosiowym urządzeniem do pozycjonowania części. Woida twierdzi, że możliwe jest tworzenie części o wymiarach 2 x 8 x 40 m.
Możliwa do uzyskania tolerancja waha się w przedziale od +/?0,5 do +/?1,5 mm w zależności od tempa osadzania materiału. Produkcja części zwykle wymaga obróbki skrawaniem. Ponadto proces obróbki addytywnej tworzy utwardzoną cieplnie warstwę materiału, więc produkcja części z metali miękkich wymaga również wyżarzania.
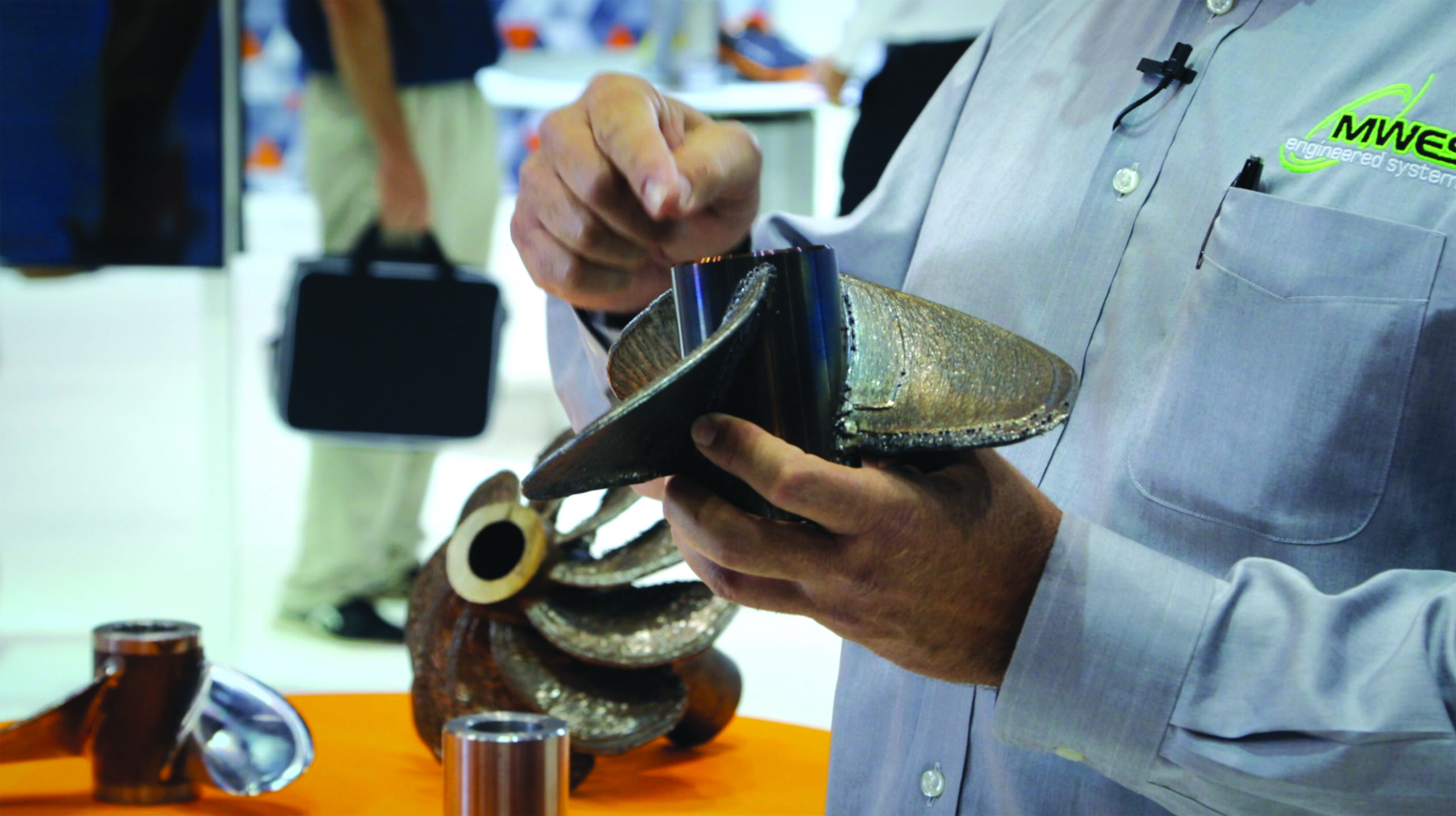
Dowolność kształtu to zmniejszenie ilości odpadów
Zalety takiego procesu to szybka produkcja nowych podzespołów z metalu, możliwość wprowadzania szybkich zmian konstrukcyjnych bez generowania dodatkowych kosztów związanych z modyfikacją narzędzi oraz niski koszt wprowadzenia części do produkcji. Woida twierdzi, że największą korzyścią jest możliwość tworzenia kilku podzłożeń i łączenia ich w jedną całość.
Posłużmy się przykładem firmy GE Avition, gdzie w sposób innowacyjny wykorzystano obróbkę addytywną do tworzenia części do zaawansowanego technicznie silnika turboodrzutowego. Inżynierowie z GE mogli dzięki temu zredukować ilość podzespołów z 855 do zaledwie 12. Ponad 1/3 wszystkich części silnika jest drukowana tą metodą.
Dzięki systemowi MWES ADDere możliwa jest produkcja elementów o dowolnym kształcie i stosowanie różnych materiałów do budowy jednego komponentu, co umożliwia tym samym uzyskanie odpowiedniej charakterystyki wytrzymałościowej do danej aplikacji. Jest to efektywne kosztowo, zwłaszcza wtedy, gdy chcesz pokryć mniej kosztowny metal droższym w celu uzyskania właściwych parametrów, jak na przykład odporności na zużycie cierne. Proces może być również stosowany do prowadzenia napraw. Wówczas maszynujemy daną część w celu uzyskania stabilnej struktury, a potem odbudowujemy ją do jej domyślnego kształtu.
? ?Osiągamy właściwości zbliżone do części odlewanych, ale bardziej odpowiadające częściom kutym? ? twierdzi Woida. ? ?W porównaniu do obróbki ubytkowej używamy mniej materiału, ponieważ kształt wytwarzanego wyrobu jest zbliżony do końcowego?.
Stosowanie obróbki addytywnej z wykorzystaniem drutu powoduje mniej strat materiału niż tworzenie części metodą obróbki addytywnej wykorzystującej proszek. Woida twierdzi, że są w stanie wykorzystać 99% zużywanego materiału.
? ?Kiedy wykorzystujemy drut do produkcji komponentów cały materiał jest zużywany do tworzenia obiektu? ? twierdzi. ? ?Występuje niewielka ilość odpadu drutu w przeciwieństwie do materiałów spiekanych z proszków, gdzie nadmiar proszku jest usuwany i musi zostać poddany recyklingowi. Jedyną czynnością jaką musimy wykonać, jest maszynowanie zewnętrznej powierzchni komponentu. Zwykle maszynowanie dotyczy jedynie powierzchni współpracujących. Nie jest konieczne maszynowanie całej części?.
Jak wyjaśnia Woida, w przypadku śruby napędowej stworzonej na stanowisku demonstracyjnym wymagane jest maszynowanie około 5% powierzchni całej części. Proces ten jest również 10 razy szybszy od procesu spiekania proszków.
? ?Możemy dodawać 15 kg materiału stali nierdzewnej na godzinę, wykorzystując laser o mocy 14 kW. Wkrótce będziemy posiadać laser o mocy 20 kW. Jeśli materiał jest drogi i trudny w obróbce ubytkowej, wówczas proces obróbki addytywnej jest uzasadniony? ? dodaje..
Proces ten nie jest jednak odpowiedni dla niewielkich komponentów oraz części, których koszt wytworzenia jest niski, oraz części, które mogą być w bardzo prosty sposób wyprodukowane z bloku litego materiału.
? ?Gotowa część ma jakość podobną do jakości części odlewanych? ? twierdzi Woida. ? ?Części można maszynować lub wykorzystać laser do wygładzenia powierzchni zewnętrznej. Jednak większość naszych klientów jest zainteresowana funkcjonalnością, a nie jakością wykończenia powierzchni?.
Kosztowne podzespoły i egzotyczne materiały
System ADDere jest dostępny jako produkt gotowy do zakupu lub też jako sama usługa wytwarzania. ? ?Projekty, nad którymi dotychczas pracowaliśmy, to głównie przeprowadzanie walidacji dla klientów odnośnie możliwości wykonania części zgodnie z ich wymaganiami? ? wyjasnia Woida. ? ?Nie rozpoczęto jeszcze masowej produkcji tą metodą, ale dostarczamy klientom próbki w celu weryfikacji możliwości systemu. Klienci oceniają je pod kątem jakości, a następnie dokonują zakupu większej ilości części lub całego systemu na własny użytek?.
Jedna z części, która obecnie poddawana jest testom w placówce badawczo-rozwojowej MWES, jest ważąca 900 kg grodź lotniskowca. Wyobraźmy sobie, że zamiast wykorzystywać cenne miejsce na składowanie części zamiennych, jesteśmy w stanie wykorzystać technologię obróbki addytywnej do tworzenia i naprawy części będąc na otwartym morzu.
System obróbki ADDere znajduje zastosowanie w przemyśle kosmicznym, budowie przekładni, w zawieszeniach pojazdów, w przemyśle stoczniowym, wojsku, przemyśle naftowym, budownictwie, w przemyśle wydobywczym, oraz w przemyśle rolniczym. Materiały wykorzystywane w tej metodzie to zwykle kosztowne metale, takie jak stal nierdzewna, aluminium, tytan, kobalt, Inconel oraz stopy wolframu.
Woida twierdzi również, że zdobyte przez nich doświadczenie w spawaniu laserowym się zwraca. ? ?Zwykle zajmujemy się rozwojem wysoko zaawansowanych system, więc mamy do czynienia z najnowszymi technologiami zarówno w branży robotyki, jak i technologii laserów? ? twierdzi. ? ?Projektowanie systemów nieistniejących w żadnym katalogu, o wysokim stopniu zaawansowania technicznego jest dla nas codziennością. Wymaga to od nas obszernego doświadczenia. Potrzeba do tego inżynierów mechaników, ponieważ system bywa bardzo złożony. Niezbędni są również programiści, aby łatwo i z powodzeniem sprzedać produkt na rynku. Niezbędni są spawacze, którzy mogą dokonać weryfikacji i zapewnić, że procesy metalurgiczne zachodzą w prawidłowy sposób. Wiele osób musi pracować razem, by proces ten działał prawidłowo.
Odlewnictwo
Produkcja addytywna i robotyka znajdują również zastosowanie w nowej, cyfrowej erze odlewnictwa przemysłowego. Technologia druku 3D powstała w 1990 roku na uczelni MIT dzięki studentowi (Jim Bredt), który pracował nad swoim doktoratem, badając możliwości druku 3D metodą inkjet.
Określenie druk 3D było pierwotnie stosowane do opisu procesu, w którym różne warstwy proszku i spoiwa ciekłego układane są w zaprogramowany wzór, tworząc obiekt 3D. Bredt twierdzi, że termin ten został stworzony przez jego promotora, a następnie przyjął się w przemyśle. Obecnie druk 3D jest zamiennie stosowanym terminem z obróbką addytywną i zawiera w sobie wiele różnych typów procesów.
Bredt, będąc dyrektorem do spraw rozwoju w firmie Viridis3D, mającej siedzibę w Woburn, w stanie Massachusett, posiada 30 lat doświadczenia w branży druku 3D, lecz nigdy nie stracił kontaktu z jego pierwszą pasją ze studiów. Zaraz po ukończeniu studiów na MIT pomógł założyć firmę Z Corp. w roku 1995. Z Corp. to pierwsza firma, która wprowadziła komercyjnie dostępną technologię druku 3D metodą inkjet. Z. Corp zostało zakupione przez 3D systems ? firmę, której założyciele wynaleźli metodę produkcji zwaną stereolitografią.
Bredt opuścił 3-D Systems, aby założyć Viridis3D w 2010 roku, kierowany potrzebą powrotu do zagadnień związanych z odlewnictwem. Jego celem była budowa drukarki 3D, która byłaby bardziej wszechstronna w zakresie stosowanych materiałów i odporna na warunki panujące w zakładach odlewniczych. Firma skupiała się na zagadnieniach przemysłu odlewniczego ze specjalizacją budowania form piaskowych.
? ?Większość komponentów, do których potrzeba drukarki 3D to komponenty, które nie mogą być wykonane za pomocą konwencjonalnych metod wytwarzania. Takimi komponentami są rdzenie, które potrafią być bardzo skomplikowane? ? twierdzi Bredt.
? ?Nasza technologia zwiększa możliwości, ponieważ można podejmować większe ryzyko przy konstruowaniu produktu. Nie trzeba wydawać wiele pieniędzy na tworzenie narzędzi. Jeśli wydrukujesz część, a ona okaże się wadliwa z powodu zbyt słabej konstrukcji, nie poniesiesz przez to dużych strat. Dzięki naszej technologii rozszerza się gama kształtów geometrycznych, które może przybierać twój produkt?.
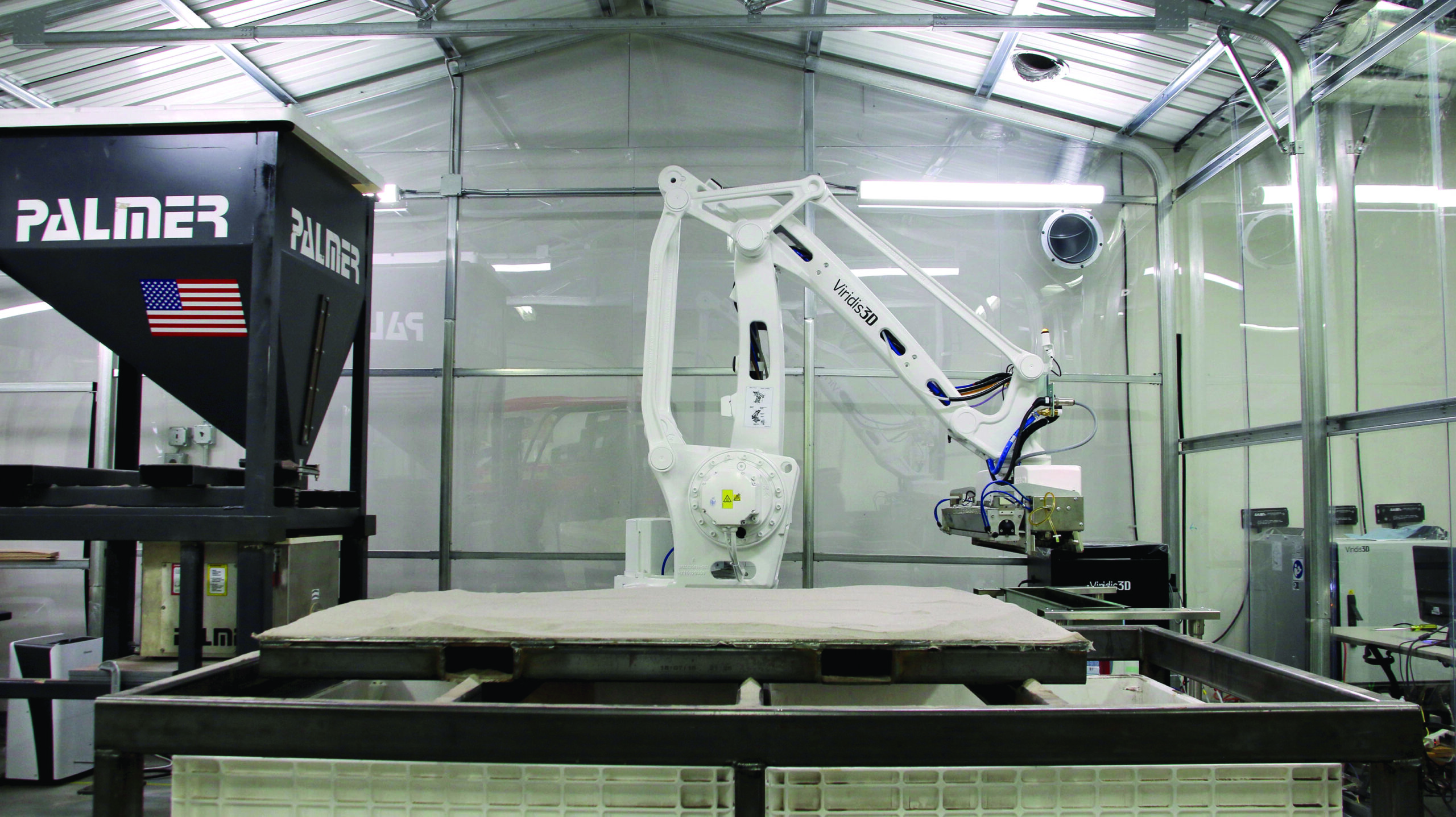
Tworzenie form
Spośród wielu rzeczy, co do których Bradt miał swoje własne przemyślenia, kwestionował on, w jaki sposób zbudowane są drukarki 3D. ? ?Drukarka 3D jest właściwie robotem z podajnikiem materiału zamocowanym na jego końcu? ? twierdzi Brandt. ? ?Kiedy tworzyliśmy firmę Virdis3D, zapytałem, dlaczego mam budować własnego robota? Moja wiedza to wiedza o materiałach, a nie konstrukcji maszyn. Dlaczego więc po prostu nie kupić robota? Wówczas mogę się skupić na procesie od strony łączenia materiałów?.
Dla firmy Virdis3D wykorzystanie gotowych i dostępnych na rynku robotów do druku 3D było przełomem wobec ich konkurencji.
? ?Wykorzystanie przez nas robotów dostępnych komercyjnie jest naszym znakiem rozpoznawczym? ? wyjaśnia Bredt. ? ?Nasi konkurenci w większości używają systemów suwnicowych do poruszania podzespołami drukującymi w przestrzeni. Dzięki wykorzystaniu manipulatora, zamiast systemu suwnicowego, nasza drukarka jest lżejsza, bardziej niezawodna oraz wytrzymalsza?.
Druk 3D z wykorzystaniem robotów
Kiedy trwał rozwój robotycznych systemów obróbki addytywnej, firma Virdis3D nawiązała współpracę z firmą ENvisionTEC, dostawcą rozwiązań do druku 3D. Obecnie w pełni wykupiona przez nią firma Virdis3D może kontynuować prace nad rozwojem technologii. Na początku tego roku Virdis3D stworzyło pierwszą komercyjną zrobotyzowaną drukarkę 3D o nazwie RAM 123.
System wykorzystuje standardowy czteroosiowy manipulator do tworzenia piaskowych form i rdzeni odlewniczych. Robot jest wyposażony w podajnik materiału (proszku), który podaje piasek, oraz głowicę drukującą, która spaja piasek ciekłym spoiwem. Poprzez odpowiednie rozmieszczenie piasku i spoiwa zrobotyzowana drukarka 3D buduje formy metodą warstwa po warstwie.
Głowica drukująca może być ciężka, zwłaszcza wtedy, gdy zawiera w sobie piasek. Bredt twierdzi, że czteroosiowy robot jest lepszy od sześcioosiowych manipulatorów, ponieważ ma większą nośność.
? ?Elementy drukujące działają tylko wtedy, gdy znajdują się w pozycji poziomej? ? zauważa. ? ?Głowica drukująca porusza się na płaszczyźnie, rzadko się podnosząc. Czteroosiowy robot jest idealny do tego zadania, ponieważ jest tak skonstruowany, by poruszał się w jednej płaszczyźnie. Ma wysoką nośność i jest bardzo dokładny?.
System RAM firmy Virdis3D ma konstrukcję otwartą. Formy budowane są na stacjonarnym stole. Podłożem jest paleta, która może być wykorzystana do przewożenia części za pomocą wózka widłowego.
? ?Nasz produkt ma otwarty stół, więc można tworzyć części różnych rozmiarów bez potrzeby wypełnienia zbiornika materiałami? ? tłumaczy Bredt. ? ?Jednym z powodów, dla których zdecydowaliśmy się na wykorzystanie stołu stacjonarnego był fakt, że jeśli budujesz coraz to większe i większe maszyny, z czasem podłoże będzie ważyć więcej niż sama maszyna?.
Krótkie terminy dostawy i oszczędność miejsca
? ?Tworzenie wzorów w formach to dziedzina na wymarciu? ? mówi Bredt. ? ?Firmy, które posiadają 50 letnie formy z wzorami, zatrudniają przypadkowe osoby do ich naprawy. W niektórych przypadkach jedyne co mają to rysunki, a czasem niezbędne jest dokonanie inżynierii odwrotnej istniejącego produktu z powodu braku dokumentacji. Klienci, którzy kupują nasz system bardzo cenią sobie opcję przejścia na wytwarzanie cyfrowe, ponieważ pozbywają się problemu przechowywania wzorów. Jest to świetny przykład zastępowania starej technologii nową?.
Brendt twierdzi, że wciąż poszerza swoją ofertę o inne materiały niż piasek, które oferują lepszą jakość rdzeni, włącznie z proszkami z tworzyw sztucznych, ceramiką, a nawet proszkami metali. Roboty wciąż będą wspomagać drukowanie, a ich wykorzystane do procesów obróbki addytywnej zmieni nasz sposób myślenia o wytwarzaniu.
Tanya M. Anadan zajmuje stanowisko Contrubuting Editor w Robotic Industries Association (RIA) oraz Robotics Online.