Drukarki 3D stanowią obecnie integralną część parku maszynowego wielu zakładów przemysłowych, w których stosowane są zarówno w procesach prototypowania, jak i wytwarzania narzędzi i produkcji małoseryjnej. Drukowanie przestrzenne to bardzo dynamicznie rozwijająca się dziedzina, oferująca coraz nowsze i doskonalsze rozwiązania mające na celu optymalizację produkcji oraz poprawę jakości wytwarzanych elementów.
Mówiąc o druku 3D, a właściwie o wytwarzaniu addytywnym, jak prawidłowo określa się tę technologię, warto wspomnieć o etapach jego powstawania, by uzmysłowić sobie, jak dobrze rozwinięta jest to branża. Pierwsze komercyjne wykorzystanie druku 3D miało miejsce w 1987 r., czyli trzy lata po opatentowaniu stereolitografii (pierwszej technologii druku 3D) przez Chucka Hulla ? współzałożyciela amerykańskiej firmy 3D Systems. Niedługo później, bo w 1989 r., S. Scott Crump opatentował technologię FDM (Fused Deposition Modelling), która obecnie cieszy się bardzo dużym zainteresowaniem. Jak podkreśla Katarzyna Musiał, Marketing Manager w firmie 3D Printers, śmiało można stwierdzić, że czasy, gdy druk 3D jawił się jako nieznana i fascynująca technologia, już dawno minęły. Wytwarzanie addytywne na dobre zagościło w naszej rzeczywistości, wychodząc poza mury uczelni i warsztaty pasjonatów. Miało to miejsce już kilkanaście lat temu, gdy wygasły patenty wynalazców, a przedsiębiorcy zaczęli inwestować w przyszłościową branżę.

Od prototypowania do wytwarzania części
Jak wynika z ankiety redakcyjnej, zastosowanie druku 3D w przedsiębiorstwach uczestników badania najczęściej sprowadza się do: szybkiego prototypowania (60%), wytwarzania funkcjonalnych części (33%) oraz wspomagania produkcji i kontroli jakości (7%).
Z obserwacji Piotra Banackiego, dyrektora sprzedaży w firmie Materialise, wynika, że technologie addytywne znajdują zastosowanie w wielu obszarach funkcjonalnych każdej organizacji przemysłowej. Powszechnie druk 3D postrzega się jako nowoczesne narzędzie wykorzystywane w procesach prototypowania przemysłowego. Niemniej jednak kilka ostatnich lat pokazuje, że technologie addytywne dynamicznie zagospodarowują procesy przemysłowej produkcji seryjnej. Trend ten widoczny jest w wielu branżach, w szczególności: lotniczej, kosmicznej czy też branży urządzeń przemysłowych. Pamiętajmy jednak, że technologie addytywne, obok bycia komplementarnymi wobec tradycyjnych technologii produkcyjnych, mają przede wszystkim stanowić krok w przód w zakresie innowacyjnego rozwiązania problemów i ograniczeń tradycyjnych technologii. Stąd szerokie zastosowanie druku 3D w produkcji jednostkowej niemalże we wszystkich branżach przemysłowych.
Chociaż druk 3D powstał z myślą o szybkim przygotowaniu prototypów, to jednak ? jak zauważa Marcin Raś, Sales Manager w firmie BLIXET ? drukowane modele można wykorzystać w różny sposób, czego przykładem są: testy funkcjonalności produktu, kontrola poprawności projektu, weryfikacja dopasowania elementów, prezentacja produktu przed akceptacją ostatecznego kształtu, odtworzenie uszkodzonych elementów, a także wytwarzanie części, w przypadku których tradycyjne metody są zbyt kosztowne lub niemożliwe do zastosowania.
Produkcja metodą przyrostową umożliwia szybkie wytwarzanie fizycznych modeli produktów lub ich części składowych, a także prototypów, w tym pozwala m.in. uzyskać kształty niedostępne w innych technologiach, zmniejszyć wagę produktów oraz zwiększyć ich wytrzymałość.
Zdaniem Damiana Żelechowskiego, inżyniera serwisanta w firmie PROSOLUTIONS, trudno jest określić jeden sektor, gdzie druk 3D znajduje zastosowanie. Przekrój firm stosujących tę technologię jest naprawdę ogromny ? od firm meblarskich, kosmetycznych, poprzez branżę automotive, przemysł elektroniczny, lotnictwo, kosmonautykę, sektor militarny oraz dóbr konsumenckich, jubilerstwo, aż do przemysłu medycznego. Większość dzisiejszych ośrodków R&D czy firm zajmujących się szeroko pojętym wytwarzaniem i/lub prototypowaniem ma drukarkę 3D. Należy również wspomnieć o różnego rodzaju wzornictwie (przemysłowym i nie tylko), sztuce, a także wytwarzaniu wyspecjalizowanych narzędzi i oprzyrządowania.
W zasadzie nie ma obszarów przemysłu, w których druk 3D nie miałby zastosowania ? wszystko zależy od kreatywności, możliwości inżynierów i otwartości na rzeczywiste innowacje. W opinii Krzysztofa Nowaka, dyrektora sprzedaży i głównego doradcy w firmie 3D Center, druk 3D może mieć zastosowanie wszędzie, gdzie projektujemy i produkujemy. To fantastyczne narzędzie i jedynie od nas zależy, czy będziemy potrafili znaleźć dla niego zastosowanie.
Jak zauważa Andrzej Burgs, CEO firmy Sygnis New Technologies, zakres obszarów, które wykorzystują druk 3D, nie zmienia się od lat. Wciąż najsilniej obecny jest w działach prototypowania, badawczych, służbach utrzymania ruchu oraz nietypowych aplikacjach. Tym zaś, co systematycznie wzrasta, jest efektywność działań i wydajność drukarek 3D. Szacuje się, że efektywność systemów druku 3D rośnie o około 15?20% rocznie. Spowodowane jest to zarówno rozwojem samych drukarek, jak i materiałów do druku oraz software?u sterującego procesami druku. Obserwując częstotliwość zmian w programach, widać, że kierunek wzrostu wydajności będzie głównym powodem zwiększenia aplikacyjności druku 3D w przemyśle.
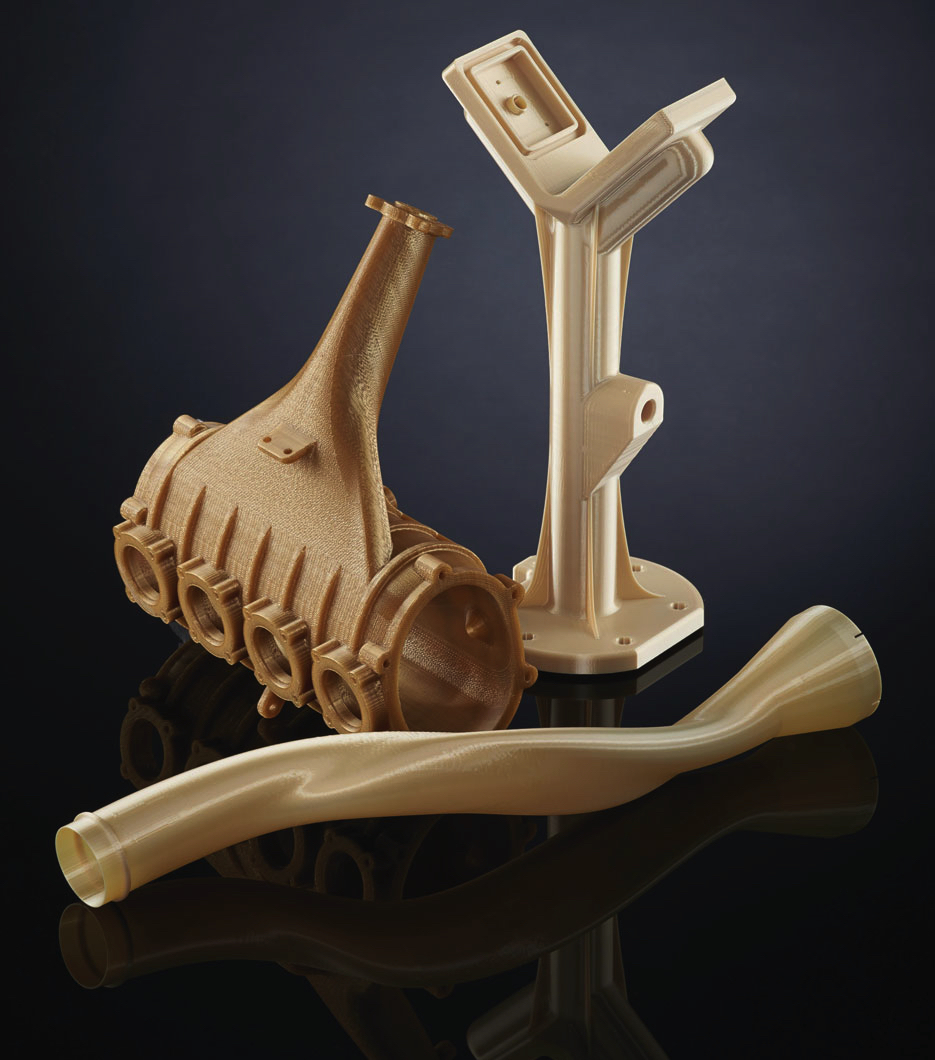
To się opłaca
Zarówno ankietowani użytkownicy, jak i dostawcy są zdania, że największymi korzyściami związanymi z wytwarzaniem addytywnym są możliwość wytwarzania części o dużym stopniu skomplikowania geometrycznego oraz krótki czas produkcji (rys. 1). Również prostota procesu wytwarzania oraz brak kosztów początkowych postrzegane są jako ogromne zalety druku 3D.
Jeśli chodzi o wytwarzanie części o niepowtarzalnej przez inne technologie geometrii, to ? jak wyjaśnia Krzysztof Nowak z firmy 3D Center ? dzięki temu możemy produkować lżejsze, bardziej wytrzymałe i tańsze elementy w bardzo krótkim czasie, właściwie na żądanie. W wielu przypadkach procesy, które trwały wiele miesięcy, można skrócić do kilku dni, co może przynieść ogromne oszczędności i zyski.
Produkcja pojedynczego detalu jest dużo tańsza niż wyprodukowanie go tradycyjnymi metodami, dlatego drukarki 3D są bardzo przydatne w procesie prototypowania, na co zwraca uwagę Paulina Kątna, specjalista ds. druku 3D w firmie PROCAD. Druk 3D pozwala na szybką weryfikację projektu pod względem założeń, sposobów montażu czy pasowania. Dodatkowo wydruki można w łatwy sposób poddać obróbce wykończeniowej (np. szlifowaniu, polerowaniu, malowaniu).
Szybkość pracy jest ? jak zauważa Adam Przepolski, specjalista ds. druku 3D w firmie CadXpert ? największą zaletą druku 3D w kontekście utrzymania ruchu. Zapasową część możemy otrzymać w ciągu kilkunastu godzin, a nie w ciągu dni lub tygodni, jak w przypadku konwencjonalnych metod wytwarzania. Dobrym rozwiązaniem jest również połączenie technologii skanowania 3D oraz drukowania 3D. Wykorzystanie inżynierii odwrotnej skraca czas dostawy o kolejne cenne godziny, które pochłonęłoby projektowanie od zera uszkodzonej części w środowisku CAD.
Druk 3D zwiększa efektywność tradycyjnych procesów wytwarzania, stanowi również świetne uzupełnienie np. dla maszyn CNC lub urządzeń będących częścią linii technologicznych.
Jak wyjaśnia Katarzyna Musiał, drukarka 3D pomaga utrzymać ciągłość pracy pojedynczych urządzeń, a nawet całej produkcji. Gdy zepsuje się lub zużyje część urządzenia, zamiast zlecać jej wykonanie i czekać dniami lub tygodniami na dostarczenie nowej, można tymczasowo zastąpić ją wydrukowanym elementem. Materiały stosowane w wytwarzaniu addytywnym, takie jak nylon lub PC ABS, mają wystarczająco dużą wytrzymałość, żeby wydrukowane części były w pełni funkcjonalne, a ich wytworzenie trwa zaledwie kilka godzin. Ponadto druk 3D daje pełną swobodę wytwarzania zaprojektowanych części, niezależnie od ich kształtu i liczby, dlatego można go wykorzystać do robienia osłon, uchwytów oraz narzędzi.
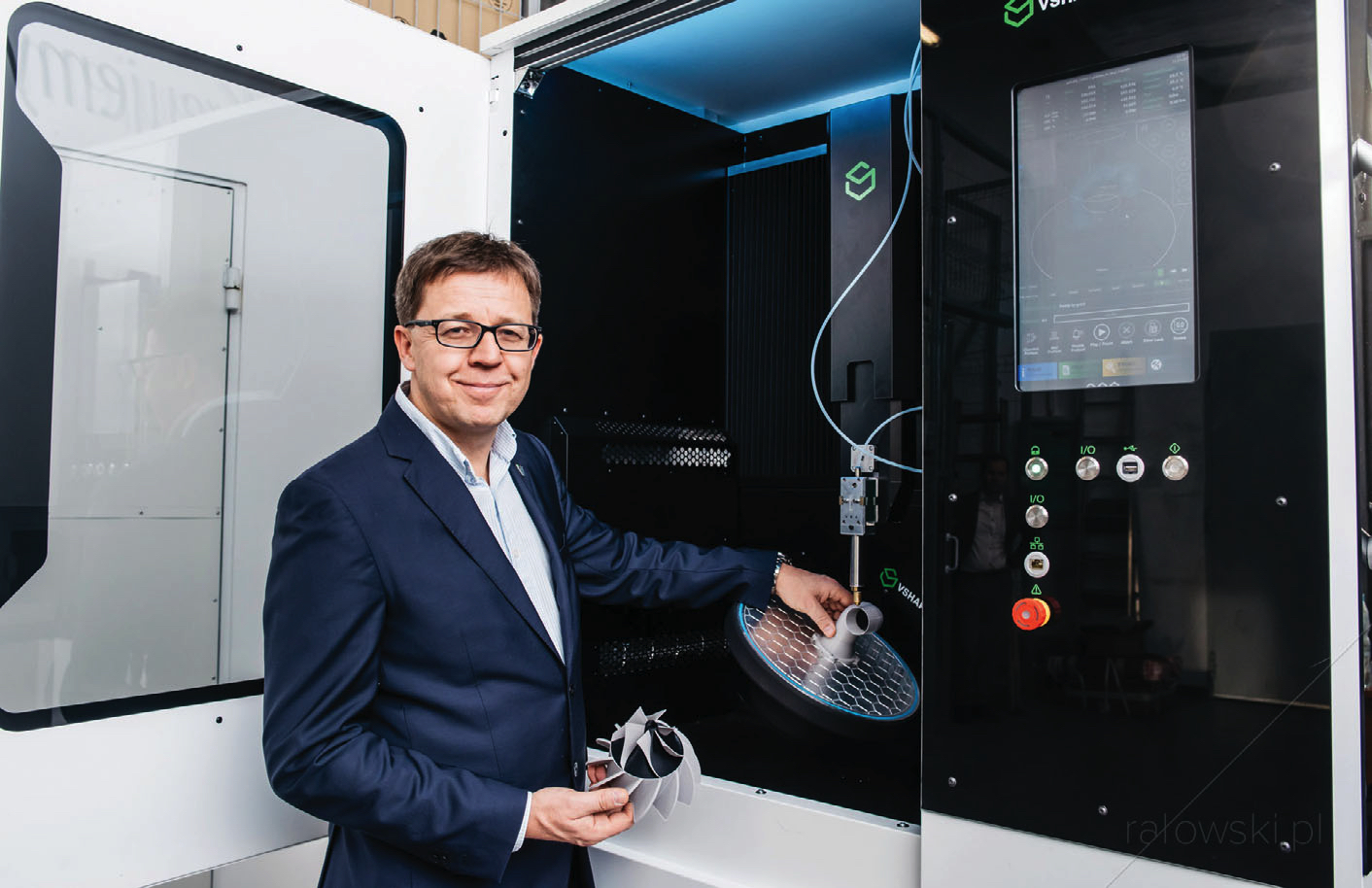
Obraz polskiego rynku
Polski rynek druku 3D jest w okresie gwałtownej zmiany, co podkreśla Andrzej Burgs z firmy Sygnis New Technologies. Ostatnie kilkanaście miesięcy przyniosło wiele bankructw, ale jednocześnie wiele rozkwitów. Wytworzyły się sprawnie działające klastry współpracy branżowej, w ramach których następują konsolidacje rynkowe. Możliwe, że na kolejnych targach branżowych będzie mniej firm, jednak będą one lepiej przygotowane merytorycznie i z większymi zasobami. Akwizycja i koncentracja wiedzy oraz zasobów będzie jednym z motorów wzrostu branży, której dotychczasowe rozproszenie mocno hamowało rozwój podmiotów branżowych. Warto tu podkreślić, że minione miesiące to debiuty pierwszych, w całości polskich konstrukcyjnie maszyn do przemysłowego druku 3D. To bardzo duży postęp techniczny oraz akumulacja wiedzy i możliwości, które będą oddziaływać na wszystkie firmy działające w obszarze profesjonalnego druku 3D.
Z obserwacji Damiana Żelechowskiego z firmy PROSOLUTIONS wynika, że rynek druku 3D stale się rozwija. W Polsce przeważają obecnie startup?y, które prowadzone są głównie przez pasjonatów druku 3D. Firmy te najczęściej oferują wydruki w przystępnych cenach. Na wyposażeniu tychże firm najczęściej znajdują się niewielkie drukarki pracujące w technologii FFF. Niemniej jednak w przypadku firm produkcyjnych czy ośrodków naukowych coraz większą popularność zdobywają profesjonalne urządzenia. Wiąże się to głównie z dostrzeganiem ogromnych korzyści wynikających ze znacznego skrócenia czasu wprowadzenia produktu na rynek (time to market) czy ? w przypadku ośrodków naukowych ? prowadzenia badań nad poprawą albo rozszerzeniem możliwości aplikacyjnych, np. poprzez określanie właściwości użytkowych wydruków.
Polski przemysł z coraz większą ufnością otwiera się na technologie addytywne, wynika również z obserwacji Piotra Banackiego z firmy Materialise. Ich dynamiczny rozwój na całym świecie promuje postrzeganie druku 3D jako jednej z technologii produkcyjnych. Niewątpliwie to co nowe wymaga uczenia się, stąd wzrastające zainteresowanie zakładów produkcyjnych przemysłowym drukiem 3D. Nadal jednak w wielu przedsiębiorstwach wykorzystanie maszyn do druku 3D istnieje w sferze testów. Wizją przyszłości pozostaje idea Przemysłu 4.0, w którym inteligentne maszyny czy roboty komunikują się ze sobą, drukując detal, który właśnie potrzebny jest w procesie produkcyjnym wyrobu finalnego. Drukowany detal jest już rzeczywistością, ale powstaje w wyniku zlecenia produkcyjnego sterowanego przez procesy produkcyjne, których integralną częścią jest nadal człowiek.
Z kolei zdaniem przedstawiciela firmy PROSOLUTIONS rynek druku 3D w obrębie maszyn do zastosowań profesjonalnych jest obecnie w fazie rozwoju, głównie w obszarze aplikacji produkcyjnych. Profesjonalne urządzenia do druku 3D gwarantują doskonałą jakość i powtarzalność wydruków przy niskiej awaryjności systemu i dodatkowym wsparciu ze strony producenta. Czynnikiem ograniczającym popyt na profesjonalne rozwiązania jest też koszt wdrożenia profesjonalnych rozwiązań, zwłaszcza w niewielkich przedsiębiorstwach. Znacznie większy postęp możemy obserwować w segmentach druku amatorskiego i półprofesjonalnego, gdzie liczna konkurencja dodatkowo mobilizuje producentów do szukania coraz to nowych rozwiązań i podążania za trendami wyznaczanymi przez uznane światowe marki.
Podobnego zdania jest Krzysztof Nowak z firmy 3D Center, z doświadczenia którego wynika, że polski rynek urządzeń addytywnych skupiony jest głównie wokół niskobudżetowych drukarek 3D (do 20 tys. zł), pracujących w technologii FDM (Fused Deposition Modelling). Natomiast w obszarze usług zdecydowanie najbardziej popularną technologią jest SLS (Selective Laser Sintering).
Rozdźwięk pomiędzy tym, jakie urządzenia kupują polscy przedsiębiorcy, a na jakich zlecają wydrukowanie modeli 3D, wynika z cen urządzeń, braku wiedzy na temat możliwości druku 3D, braku umiejętności projektowania pod druk 3D oraz braku decyzyjności w firmach o większościowym kapitale zagranicznym. Konkurencja jest duża w segmencie urządzeń niskobudżetowych FDM i SLA/DLP, natomiast wśród urządzeń z wyższej półki ilość jakościowo dobrych propozycji spada.
Polski rynek 3D najbardziej hamuje brak wiedzy na temat możliwości druku 3D i zmian związanych z nadciągającą rewolucją 4.0. W Polsce druk 3D bardzo często postrzega się jako gadżet pozwalający na wytwarzanie przedmiotów hobbystycznych, technologię przyszłości albo ? co najwyżej ? rozwiązanie umożliwiające prototypowanie. W dużym uproszczeniu polska świadomość społeczna odpowiada rzeczywistości druku 3D z 2010 r., podczas gdy mamy rok 2018 r. Tymczasem dla technologii addytywnych 10 lat to epoka.
Warto w tym miejscu zaznaczyć, że niska świadomość na temat możliwości technologii druku 3D została uznana przez ankietowanych jako główny czynnik hamujący rozwój technologii addytywnych w Polsce. Na drugim miejscu znalazły się ograniczenia technologiczne (gabaryty, jakość powierzchni, materiały), a na trzecim ? małe zaufanie do technologii (rys. 2).
Zakup a outsourcing
Lepiej kupić własny system druku 3D, czy korzystać z outsourcingu? Zdaniem Damiana Żelechowskiego z firmy PROSOLUTIONS trudno odpowiedzieć jednoznacznie na to pytanie, gdyż decyzja o zakupie maszyny na własny użytek jest często wypadkową wielu zmiennych, takich jak np. liczba planowanych wydruków czy obawa przed wyciekiem do konkurencji wzoru modelu zleconego do druku firmie zewnętrznej. Jeżeli ktoś potrzebuje jednego wydruku czy nawet 10 wydruków w ciągu roku, raczej nie zdecyduje się na zakup profesjonalnej drukarki. Z kolei jeśli przedsiębiorca planuje drukować często i zależy mu na czasie, wtedy warto rozważyć zakup własnej maszyny.
Jak radzi Marcin Raś z firmy BLIXET, decydując się na outsourcing, trzeba wziąć pod uwagę cenę takiej usługi, a także określić, czy będzie to dla firmy opłacalne, może się bowiem okazać, że kilkukrotny wydruk pod względem kosztów będzie porównywalny z zakupem mniejszej drukarki. Zwłaszcza jeżeli wydruk będzie trzeba powtarzać ze względu na jego jakość lub zmianę projektu. Jeśli natomiast jakość wydruków proponowana przez drukarki półprofesjonalne jest niezadowalająca, wtedy warto rozważyć outsourcing.
Jak radzi ekspert firmy CadXpert, outsourcing druku 3D powinni wziąć pod uwagę przede wszystkim ci przedsiębiorcy, którzy dopiero zaczynają wprowadzać technologie 3D do procesów produkcyjnych. W ten sposób mogą przetestować technologie i wybrać tę, która odpowiada wymaganiom firmy. Outsourcing druku 3D jest dobrym rozwiązaniem dla firm, dla których zbyt dużym kosztem jest utrzymanie parku maszynowego kilkunastu urządzeń pracujących w czterech najbardziej uniwersalnych technologiach druku 3D, takich jak: FDM, SLA, PolyJet i SLS. Dla przedsiębiorców zlecających pojedyncze wydruki outsourcing jest wygodnym rozwiązaniem, pozwalającym zoptymalizować koszty i czas potrzebny na eksploatację urządzenia. Wszystko zostaje po stronie usługodawcy.
Powołując się na odpowiedzi uczestników badania, 46% ankietowanych deklaruje, że stosuje na co dzień druk 3D (mają własną drukarkę 3D), a 24% osób przyznaje, że czasami korzysta z firm usługowych (rys. 3). Z deklaracji pozostałych respondentów wynika, że obecnie nie korzystają oni z technologii addytywnych, ale zamierzają je wdrożyć w najbliższym czasie (19%). W szczególności interesuje ich zastosowanie druku 3D w prototypach (74%), gotowych produktach (52%) oraz modelach pokazowych (50%). Reszta sondowanych osób nie widzi zastosowania dla tej technologii w swojej firmie (11%).
Za główne przeszkody uniemożliwiające wprowadzenie technologii druku 3D do swojego przedsiębiorstwa zostały uznane: zbyt mała paleta dostępnych materiałów, za małe powierzchnie pola roboczego drukarek 3D oraz mała precyzja wydruków.
Technologie druku 3D
Druk 3D polega na wytwarzaniu obiektów przez nakładanie kolejnych warstw materiału. Proces zaczyna się od pozyskania modelu 3D, podzielenia go na równe warstwy, a następnie wczytania tak utworzonego pliku do drukarki. Wysokość warstwy zależy od technologii, która jest wykorzystywana. Przykładowo w technologii FDM minimalna wysokość warstwy wynosi 0,09 mm, podczas gdy w Polyjet ? 0,016 mm. Każda kolejna warstwa wykonywana jest po zakończeniu poprzedniej.
Obecnie na rynku dostępnych jest ponad 20 technologii wytwarzania przyrostowego. Najpopularniejszą wśród nich jest Fused Deposition Modeling (FDM), w której tworzywo termoplastyczne w postaci drutu jest uplastyczniane, przetłaczane przez dyszę i układane zgodnie z geometrią modelu.
Coraz większą popularność zyskują metody laserowego spiekania tworzyw sztucznych i metali, jak Selective Laser Sintering (SLS), Selective Laser Melting (SLM) oraz Direct Metal Laser Sintering (DMLS). Podobną technologią jest Electron Beam Melting (EBM), w której do topienia sproszkowanego metalu używa się wiązki elektronów.
Popularną metodą jest nadal stereolitografia (SLA), czyli pierwsza technologia druku 3D, opatentowana jeszcze w 1984 roku, w której przy użyciu lasera utwardza się żywicę światłoczułą. Oprócz opisanych technologii należy wymienić Laminated Object Manufacturing (LOM) ? technologię, w której modele powstają z papieru, Direct Write, wykorzystujący materiał w postaci past, oraz Polyjet, czyli natrysk ciekłej żywicy.
Jakość ma znaczenie
Z punktu widzenia uczestników badania, będących użytkownikami drukarki 3D lub planującymi jej zakup, najważniejszymi kryteriami mającymi wpływ na wybór urządzenia są: jakość wydruku (85%), obszar roboczy (57%), cena urządzenia (54%), możliwość druku różnymi filamentami (50%), autokalibracja (37%), serwis gwarancyjny i pogwarancyjny (28%), grzany stolik oraz łatwość obsługi (26%), liczba głowic drukujących (20%), profesjonalna obsługa klienta (17%), zabudowanie drukarki (15%), marka drukarki (12%), a także czas realizacji zamówienia (4%).
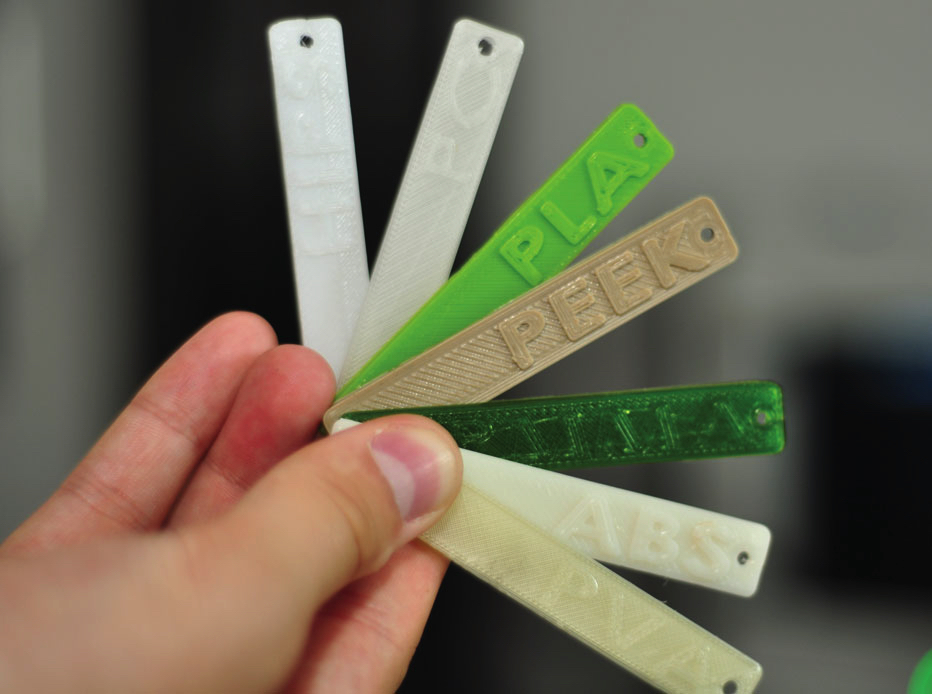
Technologie i materiały
Jak wynika z sondażu, obecnie główną technologią druku 3D stosowaną w przemyśle jest technologia FDM (Fused Deposition Modelling), która zdaniem 46% użytkowników i 90% dostawców ma najwięcej zalet. W opinii Damiana Żelechowskiego z firmy PROSOLUTIONS jest to stosunkowo tania i nieskomplikowana w swoich założeniach technologia, wykorzystująca jako materiał wyjściowy tworzywa termoplastyczne stosowane na co dzień w przemyśle. Ich dodatkowym plusem jest niska szkodliwość oraz korzystna cena. Przekrój cen urządzeń pracujących w tej technologii bywa ogromny ? od kilkuset złotych za rozwiązania amatorskie, najczęściej typu RepRap, aż do kilkuset tysięcy euro za rozwiązania przemysłowe. Główną wadą tej technologii jest jakość powierzchni uzyskiwanych modeli, którą ze względu na specyfikę technologii ciężko jest obejść bez dodatkowych zabiegów postprocesowych.
Oprócz FDM/FFF należy także wspomnieć o technologiach żywicznych, takich jak PolyJet czy SLA, nazywanej często matką technologii przyrostowych. Rozwój technologii żywicznych wynika głównie z bardzo dużej dokładności wymiarowej uzyskiwanych modeli oraz wysokiej jakości powierzchni. Z kolei ich główną wadą jest niska odporność temperaturowa (z reguły do 50°C).
Jak wynika z doświadczenia Adama Przepolskiego z firmy CadXpert, nie ma jednej idealnej technologii druku 3D dla przemysłu. Wszystko zależy od oczekiwań i wymagań klienta. Czynników w doborze technologii jest bardzo wiele. Są to m.in. geometria i wielkość modelu, dokładności wymiarowe, jakość powierzchni, właściwości materiałów.
Jeśli chodzi o wskazania respondentów, oprócz technologii FDM wiele zalet mają też SLS (37% wskazań użytkowników i 50% dostawców), SLA/MJP (37% wskazań użytkowników i 20% dostawców) oraz DMLP/MLP (30% wskazań użytkowników i dostawców). Oczywiście parametry modeli otrzymywanych przy pomocy wyżej wymienionych technologii zdecydowanie się różnią, jednak istniejące różnice absolutnie nie dyskwalifikują żadnej z nich, a jedynie mają wpływ na zastosowanie.
Przy tworzeniu modeli w technologii druku 3D użytkownicy najczęściej decydują się na takie materiały, jak np. plastiki ABS, PLA (80%), poliamid (30%) oraz fotopolimery (20%).
Jak pokazują światowe wystawy, branża eksploruje drukowanie 3D również z metalu. Najwięksi dostawcy przemysłowych systemów druku 3D inwestują w takie rozwiązania, ale wciąż pozostaje to w fazie rozwojowej. Druk 3D ze sproszkowanego metalu jest możliwy i daje zdumiewające efekty, chociaż ? jak podkreśla przedstawiciel firmy CadXpert ? wiąże się z kosztami nieosiągalnymi dla przeciętnego zakładu przemysłowego.
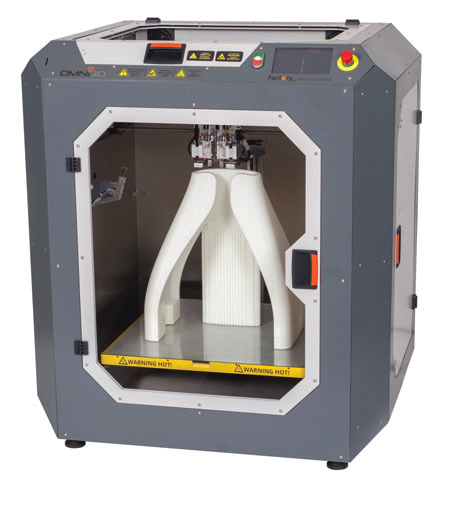
Rozwiązania profesjonalne a desktopowe
Jak zauważa przedstawiciel firmy BLIXET, drukarki przemysłowe ? w przeciwieństwie do drukarek półprofesjonalnych oraz amatorskich ? są w stanie drukować w każdej technologii, jak np. FDM/FFF, SLA, DLP, DPP czy SLS.
Ponadto sama konstrukcja drukarki do zastosowań przemysłowych jest inna. Mówiąc ogólnie, podzespoły drukarki przemysłowej są po prostu lepszej jakości, przygotowane pod duże obciążenia i długie tryby pracy (potrafią drukować nawet ponad sto godzin bez przerwy). Takie przebiegi są nie do osiągnięcia dla drukarek desktopowych. Zasilacze, podzespoły, moduły, a także sama konstrukcja są w drukarkach przemysłowych z najwyższej półki. Wszelkie elementy konstrukcyjne (takie jak np. szyny oraz
profile), nie są plastikowe, lecz stalowe, aluminiowe, ciężkie i masywne, co zwiększa możliwości przyspieszania wydruku. To wszystko sprawia, że drukarki przemysłowe umożliwiają zastosowanie praktycznie wszystkich metod i materiałów do druku, a także są przygotowane do dużych obciążeń. Wiąże się to oczywiście ze znacznie wyższą ceną drukarki przemysłowej.
Jeżeli chodzi o ceny drukarek przemysłowych, to rzeczywiście nie są one niskie. Oczywiście można znaleźć drukarkę tańszą i droższą, ale tutaj jakość i cena rzeczywiście są mocno skorelowane. Warto zwrócić uwagę także na to, że jako Polacy przodujemy w produkcji drukarek przemysłowych, a nasze produkty odznaczają się bardzo często lepszą jakością, są wyposażone w innowacyjne rozwiązania i są dużo tańsze niż wcześniej produkowane drukarki zagranicznych firm o uznanych markach.
Drukarki przemysłowe są wyposażane w zaawansowane technologie, których z uwagi na stopień skomplikowania (a także cenę) próżno szukać w drukarkach desktopowych (np. system wygładzania wydruku ? SSP czy system cichej pracy ? SilentX). Również, jeżeli brać pod uwagę wielkość pól roboczych, to drukarki amatorskie są zwyczajnie małe ? w przeciwieństwie do drukarek profesjonalnych, pozwalających na wykonanie bardzo dużego, a przy tym precyzyjnego wydruku, bez konieczności jego klejenia. Same gabaryty urządzeń sprawiają również, że układ jest sztywny i drgania powstające wokół maszyny nie wpływają na jakość wydruków.
Jak wyjaśnia Katarzyna Musiał z firmy 3D Printers, w odróżnieniu od drukarek desktopowych drukarki profesjonalne zapewniają powtarzalność wydruków ? element drukowany na podstawie takiego samego projektu będzie zawsze taki sam, niezależnie od liczby egzemplarzy. Należy też zwrócić uwagę na to, że drukarki półprofesjonalne wymagają wielu czynności związanych z obsługą urządzenia, częstej kalibracji, a mimo wszystko ciężko otrzymać na nich powtarzalność i dokładność wymiarową względem projektu.
Co istotne, ogromną zaletą korzystania z profesjonalnych systemów drukujących jest ograniczony wpływ operatora. W uproszczeniu znaczy to tyle, że rola operatora ogranicza się praktycznie do kliknięcia ?start? i czekania na gotowy wydruk. Jest to jeden z efektów stosowania zaawansowanych technologicznie podzespołów.
Jak tłumaczy Damian Żelechowski z firmy PROSOLUTIONS, maszyna po zadeklarowaniu odpowiedniego modelu, materiału wyjściowego oraz jakości wykończenia sama dobiera sobie parametry wydruku, orientację modelu, a także podejmuje decyzję o tym, czy należy zastosować podporę czy też nie. Dlatego w przypadku rozwiązań profesjonalnych materiały wyjściowe są dedykowane przez producenta, który może dzięki temu zagwarantować poprawność wykonania modelu, dobre właściwości mechaniczne oraz powtarzalność produkcji.
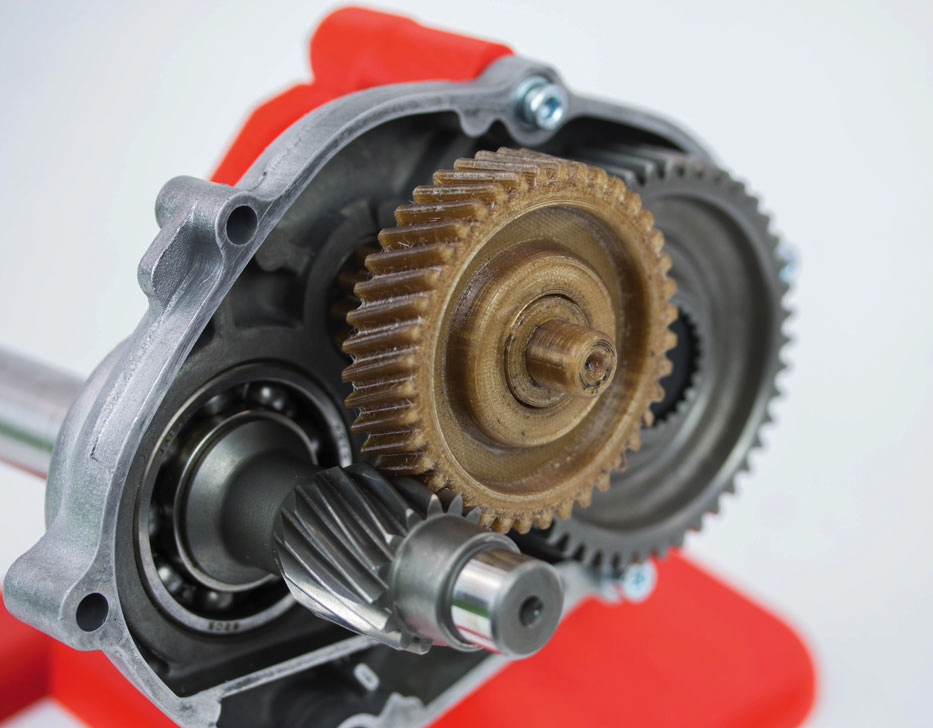
Branża Automotive
Branża motoryzacyjna jest największym odbiorcą części drukowanych w 3D. Głównym obszarem zastosowania są prototypowe części, służące do oceny wizualnej podzespołów oraz spasowania ich z karoserią, a także produkcja prototypowych modeli wystawowych. Przeprowadzane są ponadto testy ergonomiczne oraz funkcjonalne. W tym celu drukowane są części zewnętrzne, jak osłony wlotów powietrza, a nawet całe zderzaki samochodowe. Drukowane są również części wewnętrzne samochodów, w tym kierownice czy całe deski rozdzielcze. Do tego celu wykorzystywana jest przede wszystkim technologia FDM.
Drugim obszarem zastosowania technologii FDM jest produkcja narzędzi montażowych dedykowana do określonych modeli samochodu. Zaletą tak wytwarzanych narzędzi jest ich krótki czas realizacji oraz mniejsza masa niż wersji wykonanych skrawaniem. Przykład takiego zastosowania druku 3D przedstawił koncern General Motors, prezentując przyrządy dedykowane do montażu samochodu Opel Adam.
Zalety produkcji jednostkowej oraz możliwość szybkiego wprowadzania modyfikacji do modelu są szeroko wykorzystywane w sportach motorowych. Koncern BMW poinformował o produkcji kół stosowanych w pompach wody z wykorzystaniem technologii spiekania proszków metali SLM, stosowanych w serii DTM. Zespół Formuły 1 Lotus F1 Team (obecnie Renault F1 Team) informował o nawiązaniu współpracy z firmą 3D Systems (SLA, SLS) w celu wytworzenia prototypów i części koncepcyjnych przed ich wykonaniem z metalu oraz włókna węglowego. Na podobny ruch zdecydował się inny zespół Formuły 1 ? McLaren F1 Team, który nawiązał współpracę z firmą Stratasys (FDM, Polyjet Matrix).
Druk 3D wykorzystywany jest również w produkcji prototypów wystawowych czy pokazowych nowych modeli samochodów. Możliwość lakierowania elementów z tworzyw sztucznych i ich obróbka powierzchniowa mogą dać efekt zbliżony do lakierowania elementów metalowych. Koszty produkcji takich części mogą być przy tym znacznie tańsze niż złożonych kształtów z metalu.
Jest dobrze, a będzie jeszcze lepiej
Zdaniem ankietowanych dostawców obecna sytuacja panująca na polskim rynku drukarek 3D jest dobra (80%) lub nawet bardzo dobra (20%). Niemalże wszyscy respondenci uważają, że w ciągu najbliższych 12 miesięcy wzrośnie sprzedaż drukarek 3D.
Rynek druku 3D jest już dojrzały, lecz wciąż ma tendencję wzrostową. W opinii Katarzyny Musiał z firmy 3D Printers obecni użytkownicy nie zrezygnują z zastosowania technologii druku 3D. Co więcej, wszystko wskazuje na to, że zacznie przybywać firm, które zdecydują się, by włączyć ją do swoich procesów projektowania lub produkcji. Zwiększą się również nakłady na rozbudowę istniejących systemów druku 3D, które będą w stanie pokryć rosnące zapotrzebowanie na szybko i łatwo dostępne drukowane części.
Jak podkreśla Andrzej Burgs z firmy Sygnis New Technologies, świadomość klientów rośnie z roku na rok ? wiedza jest przekazywana w postaci szkoleń i dobrych merytorycznie artykułów publikowanych w czasopismach przemysłowych, a także podczas targów przemysłowych, na których od pewnego czasu standardem jest także strefa wystawców drukarek 3D. Większe zrozumienie technologii pozwala na łatwiejsze dostrzeżenie jej zastosowania w danym zakładzie produkcyjnym, co z kolei przekłada się na większe zainteresowanie i implementację przemysłowego druku 3D w poszczególnych firmach. Zdecydowanie można powiedzieć, że zainteresowanie osiągnęło co najmniej poziom średni, a duży powinno osiągnąć w ciągu 2?3 lat.
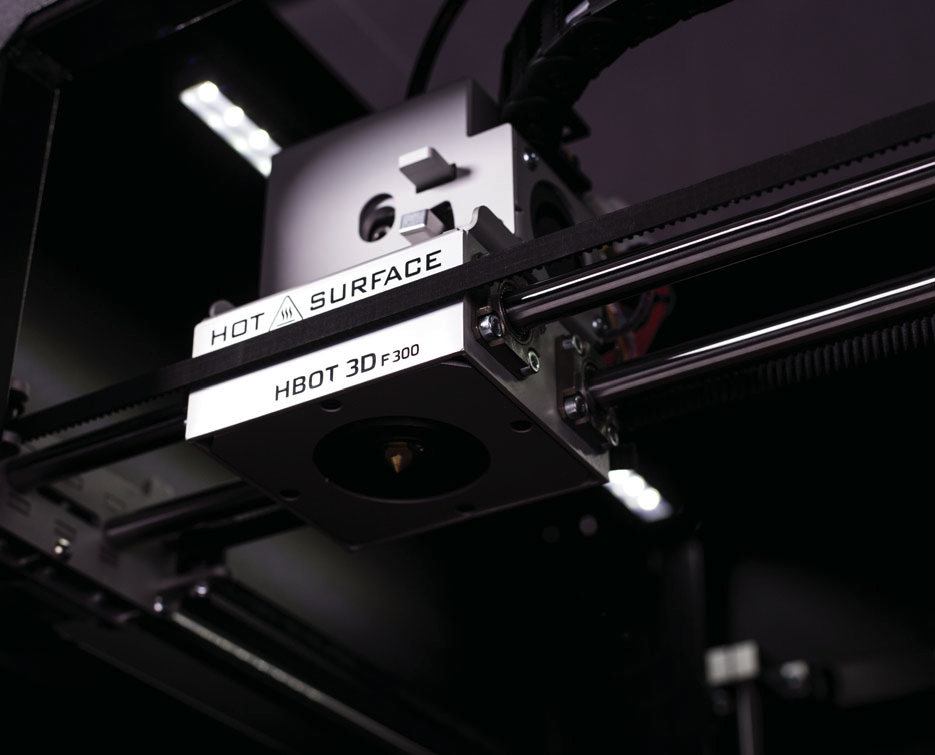
Przemysł lotniczy i kosmiczny
Pionierem w zastosowaniu druku 3D w lotnictwie jest firma General Electric. Technologie spieków metali były przez nią wykorzystywane na początku do prototypów części silników lotniczych. Obecnie prowadzone są prace nad drukowaniem finalnych części wykorzystywanych w komercyjnych silnikach lotniczych. Jako demonstrator firma wykonała działający silnik lotniczy niewielkich rozmiarów, w którym wszystkie elementy metalowe powstały w technologii wytwarzania przyrostowego. Zaangażowała się w rozwój technologii spieku metalowego tak bardzo, że w 2016 roku wykupiła dwie z trzech dużych firm produkujących drukarki 3D do metalu ? Arcam AB (technologia EBM) oraz SLM Solutions (technologia SLM). Obecnie General Electric szacuje, że do 2020 roku około 40% części silnika lotniczego może być wykonywanych w technologii 3D.
Coraz większym rynkiem dla technologii wytwarzania przyrostowego staje się również branża kosmiczna. Na Międzynarodowej Stacji Kosmicznej (ISS) stosowana jest drukarka 3D, pozwalająca na produkcję części w stanie nieważkości. Dzięki niej kosmonauci mogą wykonywać niezbędne detale na bieżąco, bez konieczności oczekiwania na przylot dostawy z Ziemi.
Drugim obszarem są konstrukcje satelitów kosmicznych, które mogą być wykonywane w technologii druku 3D. Głównymi materiałami wykorzystywanymi w tym przypadku są proszki metali, ale i materiał termoplastyczny ULTEM 9085, który uzyskał certyfikat dopuszczający go do stosowania w przestrzeni kosmicznej. Wpływa to na możliwość tworzenia skomplikowanych struktur przestrzennych, co skutkuje zmniejszeniem masy przy zachowaniu wymaganej wytrzymałości. Proszki metali znajdują zastosowanie także w silnikach rakietowych. Obecnie produkowane są części zespołu doprowadzającego paliwo do komory spalania. Przeprowadzono również testy dyszy wykonanej z proszków metalowych, zakończone sukcesem.
Druk 3D ? zagrożenie dla produkcji masowej?
Według Katarzyny Musiał druk 3D nie jest i nie będzie konkurencją dla produkcji masowej. Jednostkowy koszt oraz czas potrzebny na wykonanie (np. metodą wtrysku) elementu w partii liczącej kilka lub kilkadziesiąt tysięcy sztuk jest zdecydowanie niższy, niż wytworzenie tego samego elementu przy pomocy drukarki 3D. Sprawa jednak ma się zupełnie inaczej w przypadku produkcji niskoseryjnej lub przy produktach wykonywanych na zamówienie. Druk 3D, poza inwestycją w urządzenie, nie wymaga żadnych kosztów początkowych ? przykładowo w postaci form wtryskowych i uruchomienia linii produkcyjnej. Nie istnieje też minimalna partia produkcyjna. Wytworzyć można dowolną liczbę produktów, nawet jeśli jest to tylko jedna sztuka. Można łatwo zauważyć, że druk 3D i produkcja seryjna nie pokrywają tego samego obszaru, a doskonale się uzupełniają, co zauważyło i z powodzeniem wykorzystuje już wiele firm.
Z kolei zdaniem Andrzeja Burgsa druk 3D nie zagraża produkcji masowej ? on się po prostu stopniowo nią staje. Serie produkcyjne realizowane latami systematycznie odchodzą w zapomnienie. Teraz zmiany czy liftingi są realizowane prawie co roku. Przekłada się to na niższą rentowność m.in. wysokogatunkowych form wtryskowych, które amortyzują się na coraz krótszych seriach. Jeśli trendy personalizacji produktów będą wciąż postępować, to za kilka lat zakres kosztowy produkcji obydwoma metodami się zrówna, a w ciągu kolejnych lat druk 3D coraz częściej będzie bardziej opłacalny i elastyczny, co w konsekwencji doprowadzi do tego, że wyprze inne metody produkcji masowej, stając się metodą podstawową. W tę stronę zmierza rewolucja Przemysłu 4.0.
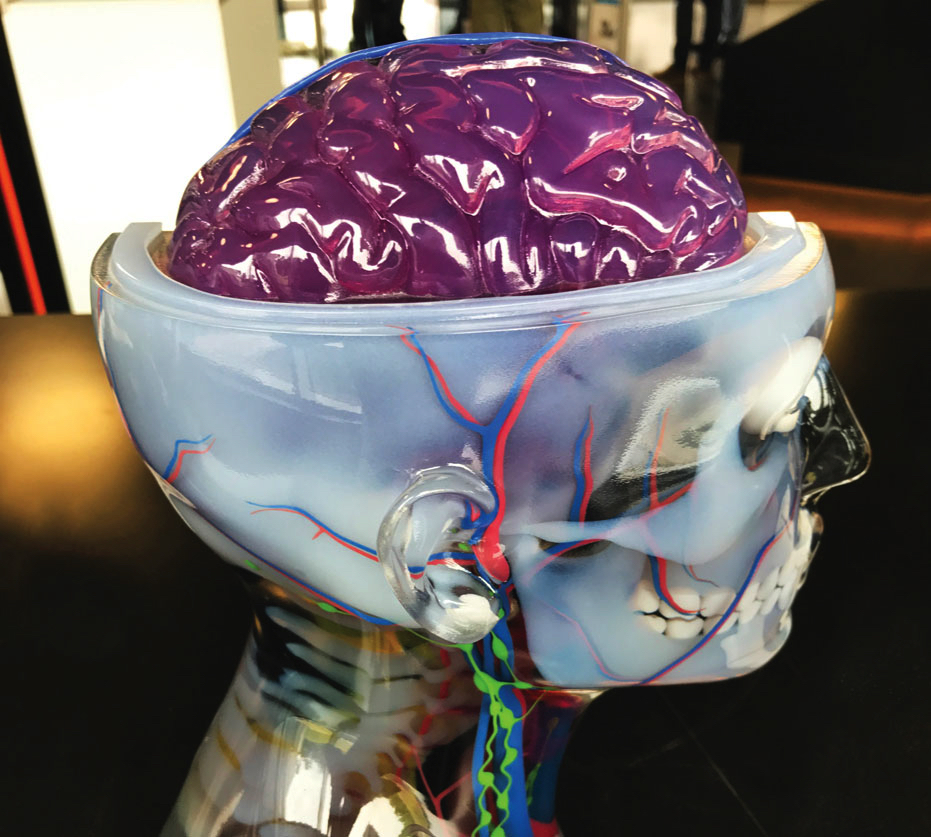
Branża medyczna
Druk 3D jest coraz powszechniej stosowany w medycynie. Pierwszym obszarem jego zastosowań są protezy. Najpopularniejszym projektem z tym związanym jest E-Nable ? projekt protezy dłoni przeznaczony do wykonania na niskobudżetowej drukarce 3D. Fundacja E-Nable działa na całym świecie, a od niedawna ma swój oddział również w Polsce.
Branża medyczna bardzo często korzysta z technologii spieku metali. W ten sposób powstają korony pod implanty zębów, na których osadzane są wkłady ceramiczne. Z tytanu spiekanego w drukarce 3D powstają implanty wszczepiane pacjentom, których kształt jest dopasowany do kości pacjenta dzięki zastosowaniu oprogramowania 3D Doctor, przekształcającego obraz z tomografu komputerowego na model 3D. Tak przygotowane implanty są gotowe do wszczepienia bez konieczności dopasowywania ich kształtu podczas operacji. Wykonywane są zarówno niewielkie płytki wypełniające, jak i gotowe implanty zastępujące usuwany obszar kostny w wyniku choroby nowotworowej. Tym sposobem uzupełnienie kostne jest gotowe jeszcze zanim chory obszar zostanie usunięty, a wszystkie czynności są wykonywane podczas jednego zabiegu.
Coraz częściej lekarze, przygotowując się do skomplikowanej operacji, korzystają z drukowanych modeli kości pacjenta. Do tak wykonanego modelu m.in. przymierzane są implanty.
Studenci medycyny mogą także korzystać z drukowanych modeli części człowieka. Wykonywane są jednokolorowe kształty w odpowiednich przekrojach, jak również wielokolorowe układy. Zastosowanie kolorowych i przezroczystych żywic umożliwiło stworzenie modelu 3D m.in. narządów z zaznaczeniem położenia żył i tętnic czy ułożenia organów i kości w ludzkim ciele.
W stronę Przemysłu 4.0
Jak wyjaśnia Tomasz Szymański, prezes zarządu w firmie VSHAPER, Przemysł 4.0 to rewolucja przemysłowa napędzana przez rozwój nowych technologii, wśród których na szczególną uwagę zasługują m.in. technologie addytywne. Za istotę tej rewolucji należy uznać zaprzęgnięcie nowoczesnych technologii do dokonania zmian w przemyśle w celu stworzenia tzw. inteligentnych fabryk, gotowych na szybkie dostosowanie się do zmieniającego się rynku i efektywne wykorzystanie zasobów. Druk 3D ? stanowiący istotne wsparcie przemysłowych procesów rapid–prototyping, rapid-tooling i rapid-manufacturing ? doskonale wpisuje się w realizację tej idei.
W opinii Tomasza Weisa druk 3D stał się wręcz niezbędną gałęzią szeroko pojętego Przemysłu 4.0. Automatyzacja procesu wytwarzania elementów jest w tym wypadku szczególnie ważna. Wyśiłki producentów profesjonalnych rozwiązań skupiają się właśnie na tym aspekcie, aby wytwarzanie elementów odbywało się z jak najmniejszym udziałem operatora.
Druk 3D pozwala na cyfryzację zasobów oraz automatyzację wielu operacji, na co zwraca uwagę również Katarzyna Musiał z firmy 3D Printers. Dotychczas wytwarzanie narzędzi lub metalowych części obejmowało cięcie, szlifowanie, frezowanie i montaż. Teraz każda z tych czynności może zostać wyeliminowana przez zastosowanie jednego urządzenia, jakim jest drukarka 3D ? zatem pojawia się jeden proces w miejsce czterech. Dodatkowo magazyny części zamiennych mogą zostać zastąpione bazą plików. Daną część można wydrukować właśnie wtedy, kiedy jest potrzebna, dlatego przechowywanie i magazynowanie traci swoje uzasadnienie.
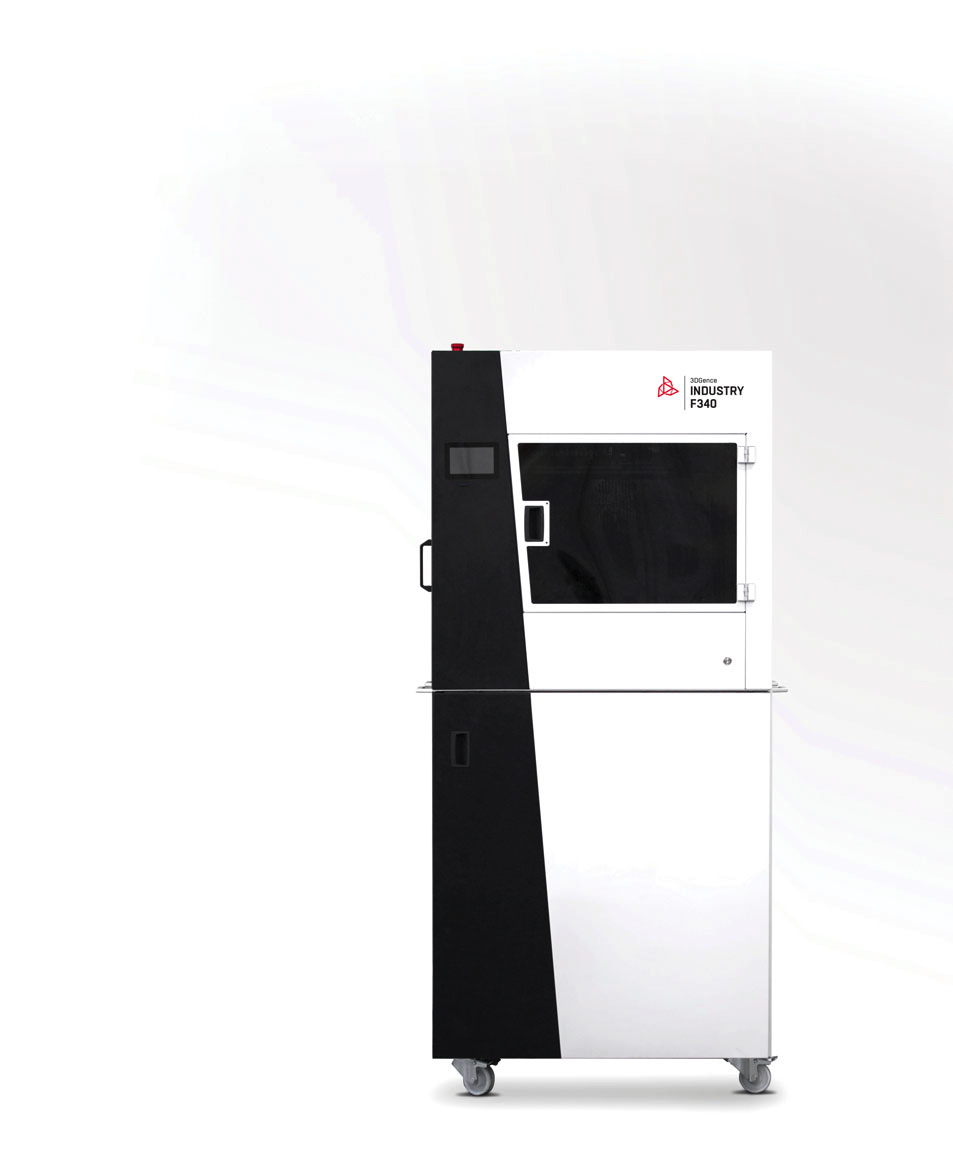
Nowe rozwiązania, nowe możliwości
Technologia druku 3D stale się rozwija. Coraz rzadziej mowa o zmianach technologicznych w samej konstrukcji drukarek 3D. Wszystko idzie raczej w kierunku nowych materiałów, zwiększenia produktywności oraz poprawy jakości wytwarzanych elementów.
Jak tłumaczy Marcin Raś z firmy BLIXET, obecnie powstają już drukarki drukujące w kolorach, kolorujące modele czy drukujące z wykorzystaniem coraz nowszych materiałów. Wydaje się, że technologia druku 3D nie starzeje się, a wciąż ewoluuje. Nie bez znaczenia jest tutaj stale poprawiająca się jakość najczęściej stosowanych filamentów oraz poszerzenie oferty filamentów bardziej specjalistycznych, jak np. PEEK, POM, NYLON czy CARBON. Dzisiaj już można uzyskiwać bardzo dobre wydruki na tych najtrudniejszych filamentach.
Oprócz tego, że będzie coraz więcej dostępnych materiałów o różnych parametrach, właściwościach i zastosowaniu, to ? zgodnie z prognozą Krzysztofa Nowaka z firmy 3D Center ? druk 3D będzie coraz tańszy, szybszy oraz będzie oferował coraz lepszą jakość
drukowanych powierzchni i otrzymywanych właściwości fizycznych wydrukowanych elementów. Ponadto w przyszłości będziemy mieli możliwość określenia nie tylko podstawowych parametrów druku 3D, ale również drukowania elementów z wielu różnych materiałów jednocześnie, o skomplikowanej strukturze powierzchni.
Zdaniem eksperta z PROSOLUTIONS druk 3D jest stosunkowo młody. Wciąż rośnie potencjał jego zastosowań a inżynierowie rozwijający tę technologię nie powiedzieli jeszcze ostatniego słowa. W jego opinii głównym trendem w rozwoju technologii przyrostowych jest możliwość stosowania wydruków jako finalnych, w pełni funkcjonalnych produktów. Już teraz istnieje taka możliwość, jednak korzysta się z niej głównie w przypadku elementów mało odpowiedzialnych (np. nieprzenoszących dużych naprężeń). Ważną ewolucją (jeśli nie rewolucją) będzie także wprowadzenie do masowej produkcji drukarek opartych na ramieniu robota, potrafiących drukować w wielu osiach. W pełni funkcjonalny prototyp takiego urządzenia, potrafiący drukować aż w ośmiu osiach, pokazała w minionym roku firma Stratasys na targach we Frankfurcie. Maszyny te pozwolą znacznie zredukować jedną z większych bolączek wytwarzania przyrostowego, jaką jest mniejsza wytrzymałość detali znajdujących się na łączeniach pomiędzy poszczególnymi warstwami. Wieloosiowość pozwoli m.in. na budowanie struktur o większej wytrzymałości mechanicznej we wszystkich osiach.
Etap, na którym obecnie znajduje się technologia druku 3D, to ? również zdaniem Andrzeja Burgs z firmy Sygnis New Technologies ? okres gwałtownego rozwoju. Istotnym światowym trendem jest wzrost liczby maszyn i technologii druku 3D z metali. Ten segment rynku druku 3D rozwija się najgwałtowniej w zakresie podnoszenia się jakości wydruków 3D oraz możliwości maszyn. W innych technologiach mamy do czynienia z optymalizacjami pracy (np. systemy SLS dwukomorowe), nowymi materiałami do druku (w maszynach SLA/DLP pojawiło się wiele zmienionych żywic o specjalnych właściwościach), a także z uproszczeniem obsługi i wzrostem niezawodności (technologie FDM ? tworzyw sztucznych). Oczekiwane jest także pojawienie się nowych technologii związanych z biotechniką ? jednak tu czas opracowania nowych, dopuszczalnych specyficznych rozwiązań to na pewno kwestia kilku lat. W wielu branżach to całkiem bliska perspektywa.
W druku 3D, silnie osadzonym w rapid prototyping, przywykliśmy, że nowe rozwiązania powstają co kilka miesięcy (np. rewolucyjne zmiany w maszynach do spieku metali). Można cytować tutaj raport Gartnera w zakresie hypercycle, że jesteśmy na krzywej wzrostu aplikacyjności, jednakże rozszerzenie się druku 3D na zdecydowanie więcej branż spowodowało, że rewolucja zmian i nowych rozwiązań trwa w najlepsze.
Agata Abramczyk jest dziennikarką, publicystką, autorką tekstów, pasjonatką nowoczesnych technologii, od wielu lat związaną z branżą dziennikarską i wydawniczą.