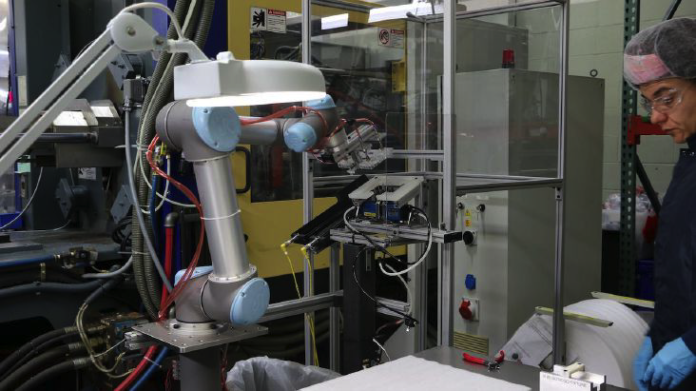
Sześć najczęstszych aplikacji robotów współpracujących to: pick-and-place, obsługa maszyn, pakowanie i paletyzowanie, realizacja zadań związanych z procesami technologicznymi, realizacja zadań związanych z wykończeniem produktów oraz kontrola jakości produktów.
Obszar wykorzystywania robotów współpracujących (ang. collaborative robots) zwiększył się znacznie w ciągu ostatnich 10 lat i obecnie jest najszybciej rozrastającym się segmentem robotów przemysłowych na świecie. W ekspansji tej prym wiedzie sześć obszarów wykorzystywania tych robotów. Najczęstsze aplikacje robotów współpracujących to: pick-and-place (podnieś i umieść), obsługa maszyn (ang. machine tending), pakowanie i paletyzowanie, realizacja zadań związanych z procesami, realizacja zadań związanych z wykończeniem produktów oraz kontrola jakości produktów. Robot współpracujący (określany też mianem kobota) to robot posiadający możliwość bezpiecznej pracy obok ludzi w celu realizacji zadań roboczych. Łatwość wdrożenia, dzięki dostępności odpowiednich technologii, jest integralna z definicją robota współpracującego.
Robot, który potrafi działać obok żywych pracowników i współpracować z nimi otwiera wiele nowych możliwości dla automatyzacji zadań w przemyśle, jednak wiele z tych możliwości może zostać niewykorzystanych w pełni, jeśli system robotyczny nie będzie łatwy do zaprogramowania, przystępny cenowo oraz wystarczająco elastyczny tak, aby mógł być szybko przestawiony na wykonywanie innych zadań.
Elastyczne systemy robotów współpracujących są obecnie wdrażane w wielu aplikacjach oraz gałęziach przemysłu na całym świecie. Poniżej opisano sześć najbardziej rozpowszechnionych aplikacji robotów współpracujących oraz podano porady na temat wdrażania tych robotów w danej aplikacji a także informacje na temat wymaganych do tego akcesoriów.
1. Roboty współpracujące, wykonujące zadania typu pick-and-place
Zadanie typu pick-and-place polega na tym, że od robota wymaga się podniesienia obrabianego elementu i umieszczenia go w innej lokalizacji lub zmiany jego orientacji. W najprostszym przypadku produkty są podstawiane robotowi w jednolitym układzie w podajniku, na palecie czy przenośniku taśmowym w przewidywalny sposób. Natomiast w bardziej skomplikowanych przypadkach wymagany jest system wizyjny, który określa orientację produktu. Zadania typu pick-and-place są doskonałymi przykładami wykorzystywania robotów współpracujących do automatyzacji produkcji w przemyśle. Przyczyną tego jest bardzo wysoka powtarzalność czynności oraz prostota ruchów robota, co czyni jego konfigurację łatwą.
Akcesoria dla robotów wykonujących zadania typu pick-and-place
Efektor końcowy. W zależności od wielkości i kształtu obrabianego elementu odpowiednia tu będzie ssawka (przyssawka) próżniowa lub chwytak. Jeśli element posiada gładką powierzchnię górną i będzie umieszczany w takiej samej orientacji jak był podnoszony, to dobrym wyborem będzie tu ssawka. Jeśli natomiast element ten nie posiada gładkich powierzchni lub musi być umieszczony w innej orientacji niż był podniesiony, to może być wymagany chwytak adaptacyjny.
System wizyjny. Jeśli produkty podstawiane robotowi w celu ich podniesienia znajdują się w pozycji lub orientacji niestandardowej, to może okazać się koniecznym zintegrowanie z robotem prostego systemu wizyjnego, który będzie wykrywał orientację danej części.
Programowanie. Programowanie aplikacji typu pick-and-place jest często nieskomplikowanym zadaniem. Wystarczy przenieść chwytak robota nad miejsce podnoszenia produktów, następnie przesunąć go nad miejsce umieszczania produktów i deaktywować efektor końcowy. W najprostszym przypadku obie lokalizacje dla czynności pick-and-place mogą być stałe. Jednak często zdarza się że jedna lub obie pozycje musza być wyregulowane za każdym cyklem, gdy są one w orientacji siatki czy stosu (może w tym pomóc funkcja paletyzowania lub szukania w oprogramowaniu). Może też być potrzebne prowadzenie wizyjne. Kamery oraz inne produkty typu plug-and-play mogą posiadać certyfikat producenta robota współpracującego. Produkty certyfikowane to: chwytaki, oprogramowanie, akcesoria oraz inne efektory końcowe i akcesoria. Produkty plug-and-play są zaprojektowane tak, aby działały bezproblemowo i przy zredukowanym czasie uruchamiania.
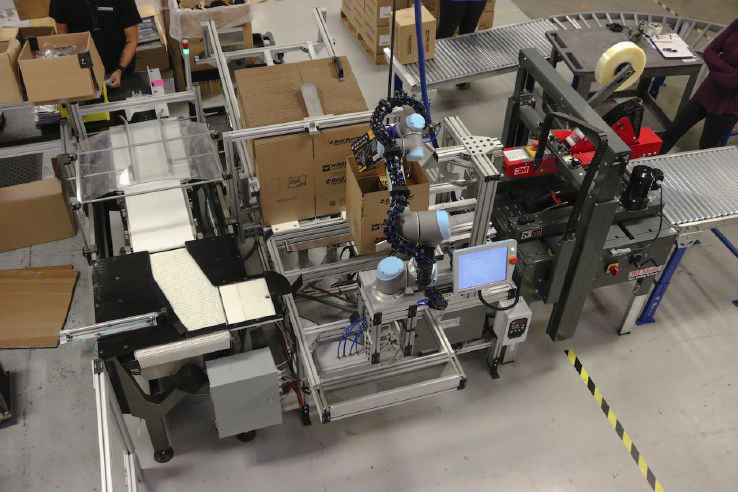
2. Wykorzystanie robotów współpracujących do obsługi maszyn
Obsługa maszyn jest innym powszechnie wykorzystywaną aplikacją robotów współpracujących. Maszyny obsługiwane przez roboty to: obrabiarki sterowane numerycznie (CNC), wtryskarki, grawery laserowe oraz prasy do tłoczenie metali. Robot podnosi surowy, nieprzetworzony produkt z podajnika, stosu, przenośnika czy jakiejś innej konfiguracji a następnie umieszcza go w ustalonej lokalizacji w maszynie.
Po wykonaniu cyklu maszynowego robot usuwa obrobioną, gotową część i umieszcza w maszynie następną surową. Jeśli cykl maszynowy jest wystarczająco długi, aby na to pozwolić, to jeden robot może jednocześnie obsługiwać kilka maszyn, co przyspiesza zwrot z inwestycji (ROI) w robota. Ze względu na małe gabaryty niektórych robotów współpracujących mogą one być często instalowane tak, aby zostawić wolną przestrzeń dla operatora. Pracownik ten może wtedy mieć dostęp do maszyny w przypadku konieczności, zaś układ hali fabrycznej pozostaje niezmieniony.
Akcesoria dla robotów współpracujących, obsługujących maszyny
Efektor końcowy. Roboty obsługujące maszyny często będą wymagały dwóch chwytaków: jednego do podnoszenia i umieszczenia surowego detalu oraz drugiego do odkładania gotowego produktu. Gdy robot podczas jednego tylko ruchu obsługuje dwie części, czas cyklu zostaje zredukowany.
System wizyjny. Jeśli produkty przychodzące do robota w celu ich podniesienia znajdują się w niestandardowej pozycji czy orientacji, to może okazać się konieczne zintegrowanie z robotem prostego systemu wizyjnego, w celu wykrywania orientacji obrabianych części.
Programowanie. Ruchy robotów obsługujących maszyny są często proste, polegające na zmianach pozycji pomiędzy produktami przychodzącymi i wychodzącymi, przy stałej pozycji maszyny. Jednak zwykle wymagane są pewne proste interfejsy We/Wy: dla robota, które umożliwiają informowanie maszyny, że obrabiana część jest juz na miejscu i cykl roboczy może się rozpocząć oraz dla maszyny, które umożliwiają informowanie robota, ze cykl roboczy został zakończony i można podać następną część do obróbki. Dla maszyn, takich jak obrabiarki CNC czy wtryskarki, będą wymagane dodatkowe sygnały do synchronizacji przekazywania obrabianej części oraz informowania maszyny, że robot znajduje się na zewnątrz maszyny, tak więc drzwiczki mogą zostać zamknięte.
Jeśli dany robot obsługuje kilka maszyn, to będzie konieczne zastosowanie pewnej dodatkowej logiki w celu podejmowania decyzji, która z maszyn ma być obsługiwana, jeśli czasy cyklu nie są identyczne.
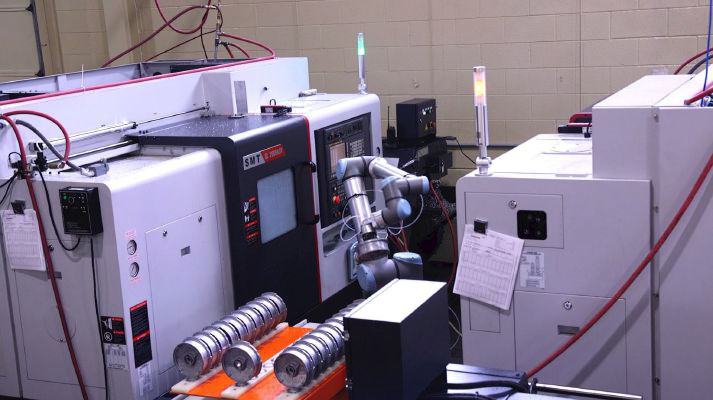
3. Roboty współpracujące, wykonujące zadania pakowania i paletyzowania
Zanim jakikolwiek produkt opuści fabrykę czy inny zakład najprawdopodobniej będzie musiał zostać zapakowany przed wysyłką. Zadania pakowania i paletyzowania mogą obejmować: pakowanie produktu poprzez umieszczenie go w maszynie do owijania w folię termokurczliwą, podniesienie opakowanych produktów z przenośnika taśmowego, posegregowanie ich i umieszczenie w pudełkach oraz umieszczenie tych pudełek na palecie dla celów wysyłki.
Produkty sztywne, przychodzące w standardowej orientacji, są łatwe w obsłudze, chociaż może być wymagany jakiś prosty system wizyjny w celu wykrywania orientacji niejednolitych części. Jeśli do robota przychodzą produkty mniej sztywne, takie jak torebki, które muszą być ciasno zapakowane w pudełka, to wymagane jest dodatkowe przeanalizowanie metody obsługi, jednak pakowanie przez robota jest nadal możliwe.
Dla firm realizujących produkcję krótkich partii wysoce zróżnicowanych wyrobów (ang. high-mix low-volume production) bardzo szybkie przestawianie się na inny produkt jest sprawą kluczową. Tak więc łatwy interfejs programowania robotów pozwala na rekonfigurację aplikacji w czasie rzędu minut.
Akcesoria dla robotów pakujących i paletyzujących
Efektor końcowy. Zadania pakowania i paletyzowania są często obsługiwane za pomocą układu ssawek próżniowych, które są wykorzystywane do podnoszenia i zwalniania produktów. W najprostszej formie mogą być one przymocowane do płyty, jednak mogą być ustawione tak, że pozycje są rekonfigurowalne, co pozwala na podnoszenie produktów o różnych wymiarach za pomocą tego samego narzędzia.
Śledzenie ruchu przenośnika. Synchronizowanie ruchów robota z ruchem przenośnika taśmowego w celu podnoszenie produktów na bieżąco jest proste przy wykorzystaniu kreatora śledzenia przenośnika. Należy podłączyć enkoder wykrywający położenie przenośnika do kanałów wejściowych w sterowniku (lub za pomocą magistrali Modbus), skonfigurować zależność pomiędzy kierunkiem a prędkością i robot jest juz gotowy do śledzenia ruchów przenośnika o zmiennej prędkości przesuwu. Jeśli jest to koniec przenośnika liniowego, gdzie produkty uderzają o zainstalowany tam mechaniczny czujnik zatrzymujący posuw, to nie jest konieczne śledzenie ruchu przenośnika, ponieważ pozycja podnoszenia jest ustalona.
System wizyjny. Jeśli produkty przychodzące do robota w celu ich podniesienia są w niestandardowej pozycji lub orientacji, to może okazać się koniecznym zintegrowanie z robotem prostego systemu wizyjnego do wykrywania orientacji danej części.
Interfejsy We/Wy. Kilka niedrogich czujników światła (fotoelektrycznych) podłączonych do sterownika pozwoli robotowi wykrywać obecność przychodzących produktów oraz pudełka, w którym ma umieścić gotowe części.
Programowanie. Konfiguracja programu dla tego typu aplikacji jest podobna jak w przypadku pick-and-place, gdy podnoszenie następuje z ustalonego położenia, będąc uruchamianym przez czujnik. Położenia umieszczania będą różniły się dla pakowania w pudełka czy paletyzowania, albo przy przesunięciu poziomym (offset) w granicach warstwy albo przy przesunięciu pionowym pomiędzy warstwami, co jest łatwe do ustawienia w oprogramowaniu. Dla bardziej złożonego wzorca paletyzacji korzystniejsze może sie okazać wprowadzenie wymiarów i lokalizacji położeń umieszczania parametrycznie, zamiast ręcznego uczenia/wprowadzania przesunięć.
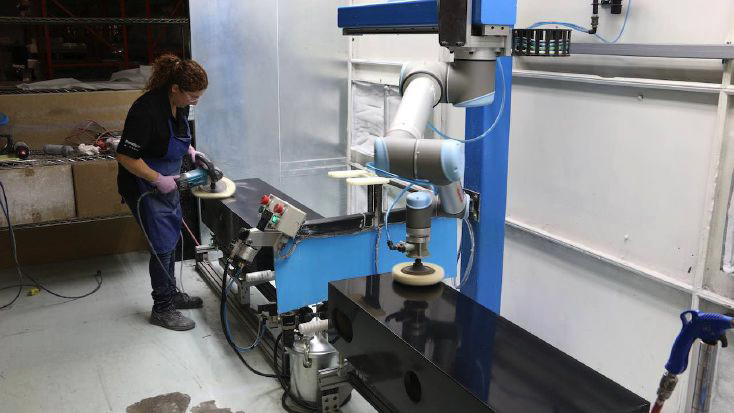
4. Zadania dla robotów współpracujących, związane z procesami technologicznymi (klejenie, dozowanie lub spawanie)
Do realizacji takich zadań związanych z procesami technologicznymi, jak klejenie, dozowanie lub spawanie, kluczowe szczegóły są takie same. Robot porusza narzędziem po ustalonej ścieżce, natomiast narzędzie to oddziałuje na obrabiany element. W każdym z tych procesów przeszkolenie nowego pracownika tak, aby mógł kontrolować liczne zmienne wymagane do uzyskania doskonałej jakości produktu, wymaga znacznej ilości czasu. Jeśli zamiast pracowników wykorzystane zostaną roboty, zaś kontrolowanie parametrów będzie kopiowane bezpośrednio z jednego robota do drugiego, to proces stanie się uproszczony.
Tradycyjny robotyczny system spawania wymaga do skonfigurowania dużej wiedzy i doświadczenia w spawaniu i programowaniu robotów. Jest on często droższy od samego palnika gazowego.
Akcesoria dla robotów wykonujących zadania związane z procesami technologicznymi
Efektor końcowy. Wymagane jest tu narzędzie technologiczne, takie jak palnik gazowy, uszczelniacz, pistolet klejowy czy dozownik pasty lutowniczej. Narzędzie to często nie musi być zaprojektowane dla wykorzystywania przez roboty, co może zredukować koszty integracji. Włączanie i wyłączanie narzędzia realizowane jest za pomocą standardowych cyfrowych sygnałów We/Wy z ewentualnym dodatkowym sygnałem analogowym, sterującym szybkością osadzania.
Programowanie. Opcja ruchu związanego z procesem, zawarta w oprogramowaniu do programowania robota, utrzymuje stałą prędkość za pomocą protokołu sterowania transmisją (TCP). Oznacza to, że jeśli narzędzie obsługiwane przez robota osadza materiał ze stałą prędkością, to system osiągnął stałe pokrycie na zaprogramowanej ścieżce. Najprostszą metodą programowania zadania procesowego jest zdefiniowanie kluczowych punktów drogowych (waypoints) w procesie wraz z promieniami mieszania (blend radius), co pozwala robotowi poruszać narzędziem wzdłuż zaokrąglonych linii na rogach na ścieżce.
Jeżeli wymaga się od systemu, aby obsługiwał dużą liczbę szybko zmieniających się części, dla których dostępne są modele projektowania wspomaganego komputerowo (CAD) oraz ścieżki procesowe modelowania wspomaganego komputerowo (CAM), to może okazać się wygodniejszym zaimportowanie tych ścieżek do programu sterującego robotem, zamiast ręcznego uczenia robota. Można to osiągnąć za pomocą pakietów oprogramowania innych producentów, które tworzą programy sterujące na podstawie danych CAD/CAM. Programy te mogą być następnie wykonane przez system robota współpracującego.
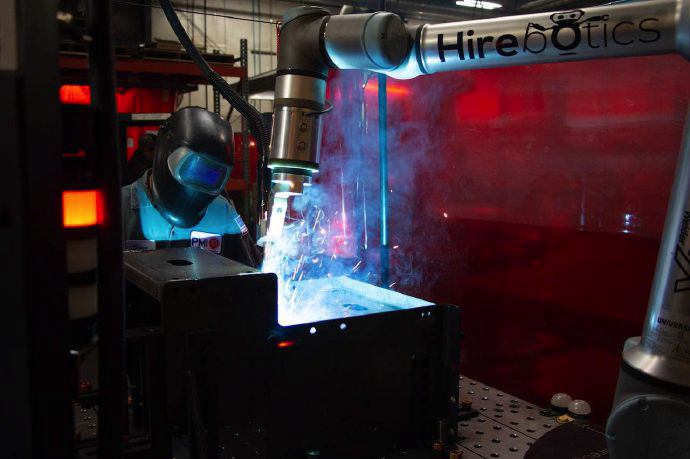
5. Zadania dla robotów współpracujących, związane z wykańczaniem powierzchni (polerowanie, szlifowanie lub gratowanie)
Wykańczanie powierzchni wymaga, aby efektor końcowy robota wywierał pewną siłę na powierzchnię obrabianego elementu, w celu usunięcia pewnej ilości materiału. Polerowanie, szlifowanie oraz gratowanie różnią się ilością, formą oraz lokalizacją materiału do usunięcia, jednak wymagania dla robota są zasadniczo takie same.
Gdy pracownik wykonuje zadanie wykańczania powierzchni za pomocą narzędzia ręcznego, często wymaga to wywarcia dużej siły na obrabiany element, co generuje znaczne drgania i może prowadzić do zranienia tego pracownika. Takich wypadków przy pracy można uniknąć dzięki wykorzystaniu robotów. Zadania związane z wykończeniem powierzchni często wykorzystują polecenia ruchu wymienione w zadaniu technologicznym, zaś robot może być albo nauczony ręcznie ścieżki realizacji zadania, bądź też informacje z danych CAD/CAM mogą być wprowadzone bezpośrednio do programu sterującego robotem.
Regulacja siły nacisku może także uczynić robota bardziej solidnym przy zajmowaniu się częściami o różnych wymiarach. Można to osiągnąć albo za pomocą czujników siły wbudowanych w robota albo montowanych na nadgarstku zewnętrznych czujników siły i momentu ? zależnie od wymaganej czułości.
Akcesoria dla robotów realizujących zadania związane z wykańczaniem powierzchni
Efektor końcowy. Dla tego typu aplikacji wymagane jest narzędzie wykańczające, które może być zaprojektowane albo do użytku ogólnego (ręczne) albo do specyficznych zastosowań robotycznych. Co prawda narzędzia ręczne są generalnie tańsze i mogą być włączane oraz wyłączane przez robota, jednak ich układy sterowania są często obsługiwane za pomocą przycisków, podczas gdy narzędzia dla robotów zawierają interfejs We/Wy do sterowania bezpośredniego.
Czujnik siły i momentu. Jeśli zadanie do wykonania wymaga regulacji siły w zakresie poniżej 1 N (na przykład polerowanie obudowy telefonu), to użytkownicy mogą rozważyć wyposażenie robota w dodatkowe czujniki do regulacji małych sił.
Programowanie. Programowanie robotów realizujących zadania związane z wykańczaniem powierzchni w swojej najprostszej formie jest bardzo proste. Wystarczy nawigowanie wzdłuż ustalonej ścieżki oraz aktywacja narzędzia w odpowiednich punktach.
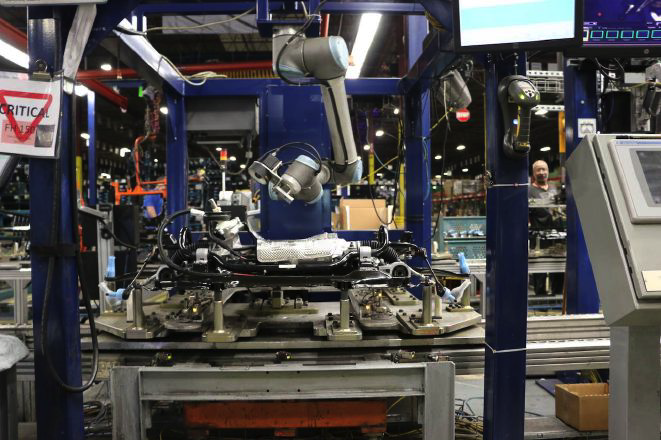
6. Kontrola jakości realizowana przez roboty współpracujące
Kontrola jakości obejmuje pełna inspekcję gotowego produktu, szczególnie będącego wynikiem precyzyjnego procesu technologicznego. Często wymagany jest przechwyt obrazów o wysokiej rozdzielczości pod różnymi kątami aby potwierdzić, że wszystkie powierzchnie i wymiary są zgodne z wymaganymi w specyfikacjach. Kamery przechwytujące te obrazy wysokiej rozdzielczości są drogie, tak więc zakup wymaganych na przykład 10 kamer do inspekcji produktu nie jest tanią inwestycją.
Jeśli jednak jedna kamera jest zamontowana na robocie i przesuwana dookoła produktu, aby osiągnąć wszystkie wymagane położenia przechwytu obrazu, to koszty takiego typu systemu zautomatyzowanej kontroli jakości znacznie spadają. W pełni autonomicznej aplikacji robot może także być wyposażony tak, aby pobierał kontrolowane części z podajnika czy przenośnika, umieszczał na stanowisku testowym i zabierał je z niego po kontroli. Wymaga to minimalnego nadzoru.
Akcesoria do kontroli jakości przez roboty
Systemy wizyjne. Głównym akcesorium wykorzystywanym w kontroli jakości przez roboty jest system wizyjny, składający się z kamery i oprogramowania do przetwarzania obrazu. Często wymagany jest tu system wyższej klasy, niż ten wykorzystywany do lokalizacji części, które ma podnosić robot. Konfiguracja systemu niekoniecznie musi być skomplikowana – dzięki coraz bardziej dostępnym algorytmom przetwarzania obrazów.
Efektor końcowy. Jeśli od robota wymaga się także obsługi części na stanowisku testowym, to na robocie obok kamery powinien być także zainstalowany chwytak do poruszania kontrolowana częścią.
Zewnętrzny przyrząd obróbkowy. Ponieważ robot umieszcza część, może on wymagać zamocowania w miejscu za pomocą przyrządu obróbkowego, w celu ustalenia położenia.
Programowanie. Konfigurowanie tego typu aplikacji jest generalnie nieskomplikowane. W przypadku, gdy robot nie musi bezpośrednio obsługiwać części, programowanie będzie obejmowało ruch do ustalonych waypointów, a następnie uruchamianie kamery za pomocą cyfrowych układów We/Wy lub komunikacji Ethernetowej. Gdy robot obsługuje części, to można tu dodać także operację pick-and-place.
Obniżanie barier dla automatyki
Opisane tutaj popularne zastosowania robotów współpracujących mogą być rozwinięte w bardzo krótkim okresie czasu, szczególnie gdy wykorzystywany jest szeroki zakres dostępnych akcesoriów plug-and-play, dostępnych wraz z niektórymi robotami współpracującymi jako część ekosystemu, w którym automatyka jest dostępna dla wszystkich.
Firmy po raz pierwszy adoptujące roboty mogą się nauczyć wielu wymaganych umiejętności dla wdrażania, wykorzystując dostępne online szkolenia dla nowych użytkowników automatyki robotycznej. Dawanie personelowi zakładu przemysłowego okazji do obsługi i programowania systemu robota współpracującego czyni wdrażanie robotyki bardziej satysfakcjonującym. Wykorzystywanie łatwych we wdrożeniu robotów współpracujących tworzy ponadto atrakcyjniejsze środowisko pracy dla nowego personelu.
Joe Campbell, starszy menedżer ds. rozwoju aplikacji w firmie Universal Robots.